PFMEA P-Diagrams
PFMEAs optionally begin with the creation of a P-Diagram. Note that by default, P-Diagrams are not enabled in Relyence Analyses. To review how to turn on P-Diagrams in your Analysis, see the FMEA Properties topic for more details.
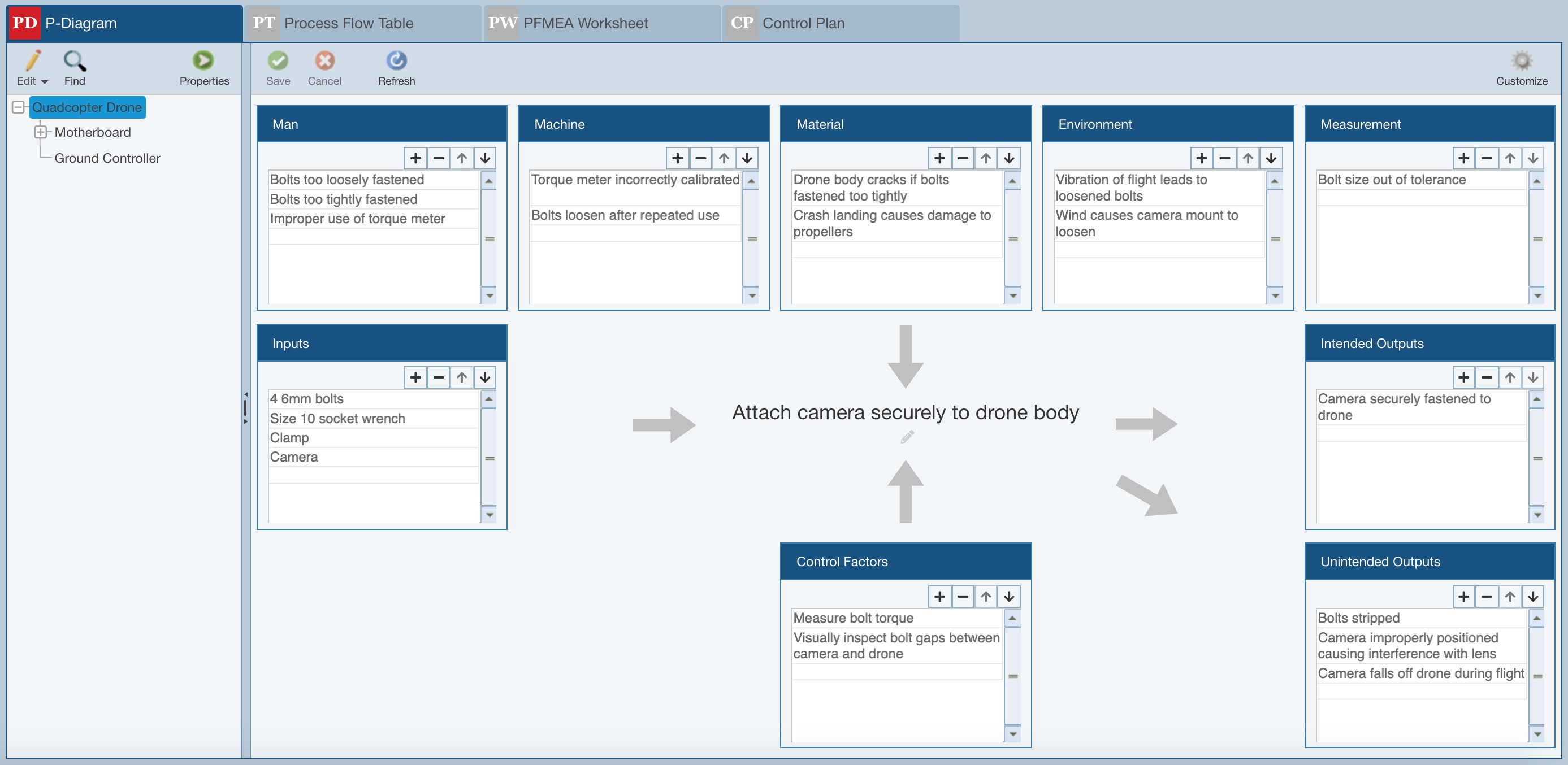
A P-Diagram, or Parameter Diagram, is a useful tool used to determine and document inputs and intended outputs for the item or process under review, along with unintended outputs (sometimes called error states), noise factors, and control factors. Function details, functional requirements, and non-functional requirements may also be documented. Developing a well-defined P-Diagram can provide useful input for the FMEA, including details like Failure Causes, Failure Modes, Effects, Current Controls, and Recommended Actions. Listed here are some additional notes to help understand the purpose and usefulness of P-Diagrams:
- Inputs are also referred to as Input Signals, Signals or Signal Factors.
- Outputs indicate the Intended Outputs. Unintended outputs, also called error states, may also be documented; these will often correlate to the Failure Modes in the FMEA.
- Noise Factors are issues or circumstances which cannot be controlled by the design or process engineers. For example, Ford defines five basic sources of noise: Piece to Piece Variation, Changes Over Time/Mileage, Customer Usage, External Environment, and System Interactions. The AIAG & VDA FMEA Handbook defines four basic sources of noise: Man, Machine, Material, and EnvironMent. Other sources suggest another noise factor as Measurement.
- Control Factors are ways to offset Noise Factors.
Note that two very useful references where you can find details about P-Diagrams include:
- Ford FMEA HANDBOOK VERSION 4.2
- AIAG & VDA FMEA Handbook