Product manufacturing combines an advanced array of technological components along with knowledgable personnel to operate, support, and maintain production line equipment. All of these entities must be finely tuned in order to maintain not just high throughput, but also high-quality output.
For success in manufacturing, a commitment to reliability, quality, and safety are of utmost importance. Without a strong effort to keep production lines at peak capacity, business can dramatically suffer. When production halts due to failure, it can lead to a cascade of detrimental effects. For this reason, the best manufacturers continually work to ensure reliability and quality throughout the organization.
Relyence supplies manufacturers with comprehensive software tools to effectively evaluate and manage quality. With Relyence software, you can be assured that your production line remains at peak performance.

Manufacturers Must Keep Reliability and Quality at the Forefront
The smooth operation of assembly lines means not only keeping the line up and running, but also ensuring product quality remains consistent and operators remain safe from hazards. Therefore, keeping product manufacturing at top performance to meet all objectives involves the range of RAMS (Reliability, Availability, Maintainability, Safety) principles.
Manufacturers recognize the importance of availability, or keeping the line up and operational as much as possible. Downtime in production leads directly to work stoppage and loss of revenue. Organizations dependent on product delivery value high availability and work to achieve this goal. It is vital that manufacturers don’t adopt a solely reactive approach to failures (fixing upon failure), but adopt preventive and predictive maintenance measures in order to avoid and mitigate failures. Optimal maintenance plans lead directly to improved availability.
Additionally, reliability is a key component for manufacturing success. Even if production line remains at peak capacity, if the resulting product is not reliable upon delivery, the business is negatively impacted.
Lastly, it is critical that safety remains a top priority as well. Not only in terms of keeping manufacturing line operators safe at all times, but ensuring that safe products are produced.
Meeting the Reliability & Quality Goals of Manufacturing with High-Powered Analytical Tools
How do manufacturers ensure that the RAMS goals are established and achieved? Implementing a strong suite of analytical software tools to organize and manage all aspects of reliability and quality programs provides a solid foundation for manufacturing success. Relyence offers products designed to work on their own or as an integrated suite — known as the Relyence Studio — to help you meet these goals and overcome common industry challenges. Our analytic tools include:
- Failure Mode and Effects Analysis (FMEA): Relyence FMEA software provides a platform for performing one of the most widely accepted reliability engineering practices: failure mode and effects analysis. By evaluating all potential failure modes and their resulting effects, you can zero in on high risk areas and make plans to avoid, detect, and mitigate them. FMEA is a proven, invaluable tool for manufacturing practices.
- Failure Reporting, Analysis and Corrective Action System (FRACAS): With Relyence FRACAS/CAPA, you can track customer complaints, failure reports, safety and compliance issues, audit reports, NCRs (nonconformance reports), and more. FRACAS enables you to track incidents of any kind from initial report to final close-out using a well-organized, manageable, and trackable approach.
- Fault Tree Analysis (FTA): Relyence Fault Tree enables you to evaluate high-risk events in a logical tree diagram. The highly efficient mathematical back-end engine computes a variety of key metrics that allow you to ensure system safety.
- Reliability Block Diagram Analysis (RBD): Relyence RBD combines graphical front-end system modeling with a back-end calculation engine to analyze complex system models, including those that incorporate redundancy.
- Reliability Prediction: Relyence Reliability Prediction performs MTBF analysis of electromechanical systems. Based on a number of accepted prediction standards, this analytical tool provides important data to allow you to improve product reliability.
- Weibull Analysis: Relyence Weibull performs life data analysis, which can be used to help foresee trends and determine your product warranty terms.
- Accelerated Life Testing (ALT) Analysis: If you perform accelerated life testing, Relyence ALT analyzes the captured data to understand how your product will perform over its lifetime.
- Maintainability Prediction: Relyence Maintainability Prediction enables you to get a metric-based assessment of your maintenance and repair tasks in order to evaluate effectiveness.
- Reliability Centered Maintenance (RCM): Using the unique reliability centered approach to maintenance planning, Relyence RCM helps you to develop optimal maintenance strategies that balance reactive, preventive, and predictive maintenance and repair activities.
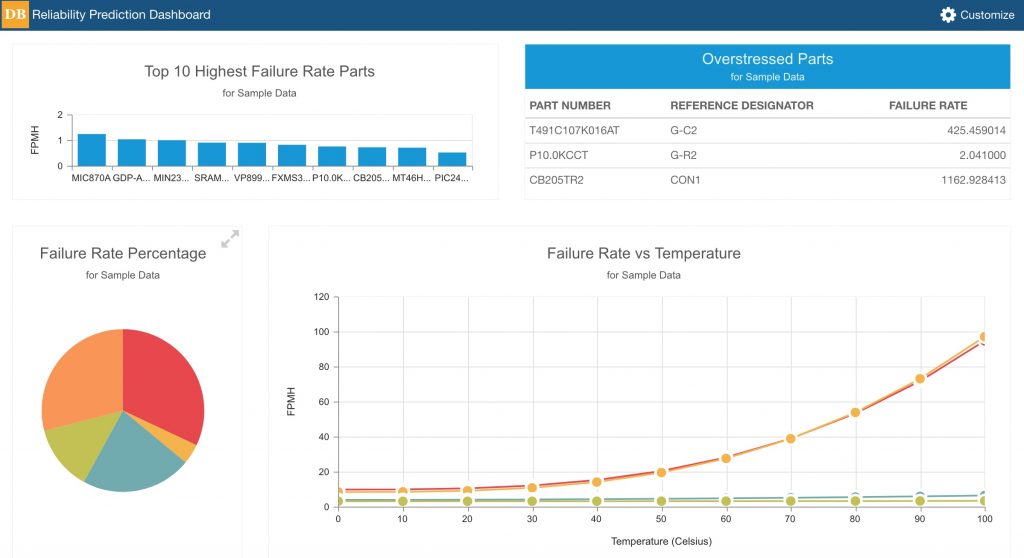
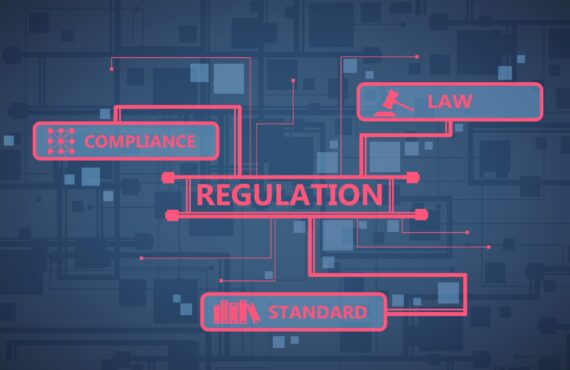
Standards to Maintain Compliance and Meet Requirements in the Manufacturing Sector
In order for reliability analysis to be complete, the entire process must meet all applicable industry standards and requirements. Some of the most often used standards include:
- SAE J1739, ARP5580, AIAG & VDA, MIL-STD-1629: The (Society of Automotive Engineers), AIAG (Automotive Industry Action Group), VDA (Verband der Automobilindustrie), and the US Department of Defense have developed FMEA (Failure Mode & Effects Analysis) guidelines that are widely accepted and used throughout the world across all industries.
- ISO and ANSI: ISO 9001 and related quality standards such as ISO/TS 16949, and ISO 14001 are some of the standards most commonly accepted and adhered to in the manufacturing sector. ANSI standards, such as ANSI/VITA 51.1, provide guidelines for reliability and quality measures.
- Six Sigma: Six Sigma quality practices and procedures are often used by manufacturers to provide effective and proven quality control measures.
- SAE JA1011 and JA1012, MIL-HDBK-2173, NAVAIR 00-25-403: These RCM (Reliability Centered Maintenance) standards offer guidelines for best practices for developing a successful maintenance program for your manufacturing process.
- Telcordia & MIL-HDBK-217: Telcordia SR-332 and MIL-HDBK-217F Notice 2 provide hardware and electronic device reliability prediction procedures that are used across a broad range of industry sectors.
Relyence’s reliability analysis software supports all these standards so that your analyses are compliant with your manufacturing organization’s requirements.
The Relyence Advantage: The Complete Tool Suite to Meet Manufacturing Reliability and Quality Goals
The Relyence tool suite is best-in-class due to its highly intuitive design and innovative feature set. Just a few of our unique advantages include:
- Browser-based accessibility: Relyence’s browser-based capability means your analysis tools are easily accessible throughout your organization, and are installation-free.
- Customizable Dashboards: Keeping tabs on your performance metrics is easily achieved using Relyence’s cross-product Dashboards. Information is accumulated and presented in a visually impactful, easy-to-understand format, and Dashboards support drilldown features for more in-depth data review.
- Tool suite integration: All Relyence tools are built on the same framework, allowing for seamless data sharing and smooth transitions between products.
- Relyence-only features: Relyence continues to lead in innovation by providing uniquely powerful capabilities including Knowledge BanksTM for efficient data reuse, FMEA Data AutoflowTM and SmartSuggestTMfor unparalleled handling and management of FMEA data, Failure Direct ConnectTM for unprecedented data sharing between FMEA & FRACAS, and Always-in-syncTM to ensure PFMEA consistency. Many of these Relyence innovations help to ensure compliancy and improve efficiency.
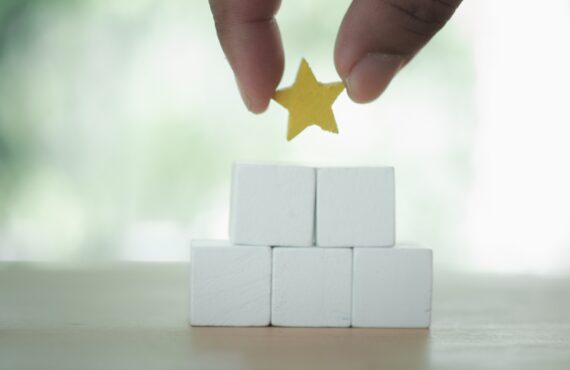
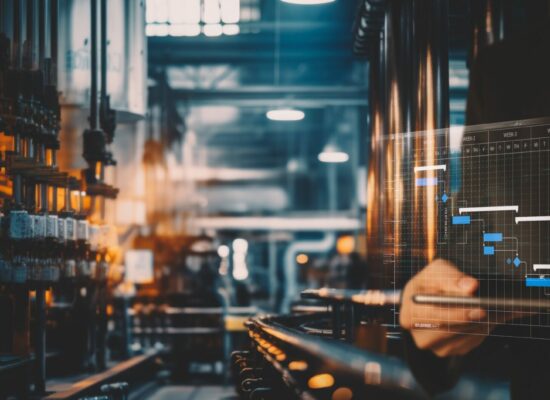
What to Look for in Your Manufacturing Reliability & Quality Analysis Tools
Your manufacturing success depends on a commitment to reliability and quality. Determining which reliability analysis software tools you employ is key to ensuring that success. To make this decision with confidence, here are some features you should look for in your reliability analysis tools for manufacturing:
- Compliancy: Whatever industry sector you are in, maintaining compliancy with external or internal requirements is crucial. Make sure the tools you select support the accepted standards and the vendor is committed to updating your tools as standards are updated.
- Built with today’s technology: Make sure your reliability analysis software is built using the most recent technology trends. Outdated software leads to frustration, poor performance, and inefficiency. Make sure your tool set of choice is kept up-to-date as the technology landscape changes.
- Support that is knowledgeable and responsive: There is no substitute for responsive and knowledgeable support. It is important to look beyond the feature set to make sure the team supporting your tool of choice is customer-driven.
- Products that are continually updated: Technology changes, best practices evolve, standards are updated. Make sure your toolset is updated on a regular basis to always be in step with the latest trends. Also, make sure the vendor listens to customers and implements suggestions for improvement.
- Multiple, integrated analysis tools: Choose software from a provider that offers a full software suite, so you can expand the tools you use as your business grows. Even if you only use one analysis tool now, your needs may change, or quality improvement efforts may lead to new analysis requirements.
What Our Customers Say About Us
Subscribe to Our eNewsletter
In addition to providing top-notch products, our dedication to delivering an outstanding customer experience is unparalleled. That’s why we encourage you to reach out to us with questions. And, please subscribe to our eNewsletter to keep up-to-date with what’s happening in quality and reliability in manufacturing.
Relyence Advisor: Tools & Tips for the Reliability and Quality Professional
Note: You can unsubscribe at any time.
Request a Free, No-Obligation Trial
In addition to providing superior products, we also deliver an outstanding customer experience. That’s why we encourage you to contact us with any questions; sign up for a free, no obligation-trial; or request a free quote today. Remember: Relyence is committed to helping you meet your reliability goals.