What is Maintainability?
Maintainability is the measure of how quickly and easily a product or system can be repaired in order to return to an operating state after a failure has occurred. Maintainability is an important aspect in overall system continuous improvements efforts, along with reliability, safety, and other factors vital to overall product viability. In fact, many times the term RAMS (Reliability, Availability, Maintainability, and Safety) or “reliability and maintainability” will be used.
Maintainability encompasses a range of activities to keep systems up and running. For example, repair and maintenance related functions may include:
- Repairing a defective component
- Replacing a defective component with a spare
- Isolating and replacing the defective parts of a component while being able to keep the working parts
- Performing maintenance activities during downtimes to prevent future failures
- Replacing components with newer designs to prevent potential failure occurrences
- Changing out components with those that are easier to repair or maintain
- Replacing worn out components
- Replacing components nearing the end of their useful life
The Importance of System Uptime
While an important aspect of system success depends on the measure of reliability, or the failure profile, of a product, it is equally important to consider the repair, or maintainability, procedures performed. For example, if a component of your system fails, but can be repaired quickly, your overall downtime is minimized. So, even though you experienced a system failure, you are able to quickly return your system to an operating state with little impact to your customers. You can see how this can be crucial in areas such as keeping military aircraft able to fly, communication networks operating, or life-saving medical devices up and running.
In many cases, maintainability is a part of continuous improvement objectives. For example, you may be able to improve the ability to repair your system by reviewing current practices, or even improve the reliability of your system based on your repair data. The lessons learned from your repair and maintenance efforts can be useful in finding ways to continually improve your product.
For these reasons, organizations invest not only in providing high reliability, but also in achieving high availability, which takes into account repair, or maintainability, metrics.
What is Maintainability Prediction?
Similar to the way Reliability Prediction evaluates failures, Maintainability Prediction evaluates repairs. For example, if a system fails but can be repaired quickly, then system uptime, or availability, is high. For this reason, an important part of assessing your product or system availability must incorporate your repair and maintenance times.
System uptime and availability depend not just on high reliability, but also on an effective maintenance program – one that includes corrective and preventive measures and ensures fast and efficient repair procedures. Quantifying and tracking maintenance activities is a critical component in ensuring your reliability and quality system goals are attained. That’s the core capability of Maintainability Predictions – providing detailed analysis and measurement of your most vital maintenance actions.
Why perform Maintainability Predictions?
Maintainability Prediction is a way to analyze a system to determine repair and maintenance measures, such as MTTR (Mean Time To Repair). MTTR and other metrics, such as MCMT (Mean Corrective Maintenance Time) and MPMT (Mean Preventive Maintenance Time), are the most common indictors used in maintainability analysis.
A Maintainability Prediction analysis uses mathematical equations to determine maintainability metrics. The calculations are based on the tasks needed to complete a maintenance activity and their associated times. Typically, this analysis is done using a software tool designed for Maintainability Prediction. Because MTTR is one of the critical metrics computed when using these analysis tools, they are sometimes referred to as MTTR software tools.
One of the main advantages of Maintainability Predictions is that they can be performed during the product design stage, enabling you to preview likely maintainability metrics. You can use this information to optimize your maintenance and repair activities to keep your system up and running with minimal downtime once it is in the field.
Performing Maintainability Predictions also enables you to focus on the review of your repair and maintenance procedures. By providing an organized and efficient approach to analyzing your system maintainability, you gain more insight and can proactively work towards improvement.
What are the Maintainability Prediction Standards?
There are several standards that focus on the topic of maintainability. There are also discussions and materials available centering on the idea of Design for Maintainability (DFM).
MIL-HDBK-470A is a Department of Defense (DoD) handbook entitled Designing and Developing Maintainable Products and Systems that includes a wealth of information to guide you in designing with maintainability in mind.
NASA-TM-4628, Recommended Techniques for Effective Maintainability, also delves into the methodologies for designing highly maintainable systems.
The most commonly used standard for performing Maintainability Predictions is MIL-HDBK-472, titled Maintainability Prediction. MIL-HDBK-472 has its roots in DoD applications but is the singular standard that has long been in place for optimal maintenance analysis across a broad range of industries worldwide.
MIL-HDBK-472 offers a detailed, analytical approach to assessing your maintenance-related metrics. This comprehensive handbook offers mathematical equations to assess the most commonly used repair measures for an accurate overview of your system maintainability profile.
What type of information do I get from Maintainability Predictions?
MTTR and Repair Metrics
MTTR (Mean Time To Repair) is the average time needed to repair a failed item. It is expressed in terms of hours. Other metrics that can be obtained from Maintainability Prediction MTTR software based on MIL-HDBK-472 include:
- MCMT: Mean Corrective Maintenance Time
- MPMT: Mean Preventive Maintenance Time
- MAMT: Mean Active Maintenance Time
- MMH/Repair: Mean Maintenance Manhours per Repair
- MMH/MA: Mean Maintenance Manhours per Maintenance Action
- MMH/OH: Mean Maintenance Manhours per Operating Hour
- MaxCMT: Maximum Corrective Maintenance Time
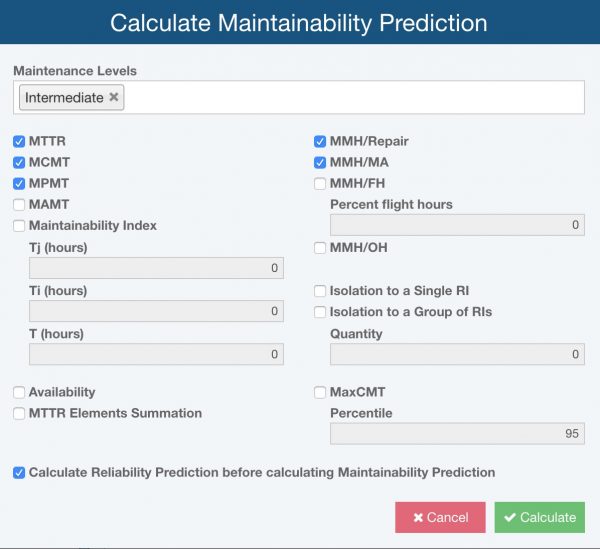
Relyence Maintainability Prediction supports a wide range of maintenance and repair metrics.
Maintenance activities can be corrective, meaning they are performed in order to fix a failure, or preventive, meaning they are performed in order to keep your system in good operating condition to avoid a fault. An example corrective action would be replacing a condenser unit in your HVAC system when it fails. Replacing the air filters in your HVAC is a preventive action – you do this to avoid a HVAC system failure due to restricted air flow.
When evaluating system availability, both types of actions need to be taken into account for accurate metrics. Maintainability Prediction analyses support the ability to define any type of maintenance activity that has an impact on your overall system uptime.
What are the benefits of performing Maintainability Predictions?
There are many advantages to performing Maintainability Prediction analysis. The central goal is to optimize your repair and maintenance policies and procedures. It is difficult to achieve this goal without measurable statistics.
It can be especially difficult in the design stage of the product lifecycle to assess repair metrics when actual production has not yet started. In this case, Maintainability Predictions are helpful by allowing you to complete an evaluation of your product prior to manufacture – while design changes that improve repair times are significantly less impactful.
Maintainability Prediction analysis can also be performed once a system is up and operational. By evaluating all the corrective and preventive maintenance actions across your system, a Maintainability Prediction analysis can provide insight into the activities or components that are causing long system downtimes. Unacceptable downtimes could be caused by a number of issues such as poor repair procedures, inability to correctly isolate a fault, or inefficiencies that cause the repair process to be too cumbersome or difficult to perform. Maintainability Predictions can help in evaluating all these factors and provide insight to enable you to improve.
Maintainability Predictions can be used starting from early phase design concept through to manufacturing and production. In fact, Maintainability Predictions are most useful when used throughout your entire product lifecycle and even into next-gen product development. You can start your prediction with as much information as you have, get a quick, early assessment, then refine your analysis as your design matures to get a more and more accurate assessment. As you then move onto future product revisions, you can start with your original analysis and adapt the lessons learned into your next design. In this manner, Maintainability Predictions become a key element in your continual improvement process.
An Overview of MIL-HDBK-472
Elements of MIL-HDBK-472
Maintenance Tasks, Maintenance Task Groups, FD&I Outputs, and Maintenance Groups
There are a number of components in performing a Maintainability Prediction analysis based on MIL-HDBK-472 methodology: Maintenance Tasks, Maintenance Task Groups, FD&I Outputs, and Maintainability Groups.
Maintenance Tasks and Maintenance Task Groups
Maintenance actions are defined by a list of basic Maintenance Tasks that define the procedure for repair or maintenance action. For example, something as basic as “remove screw” may be a basic task. Along with this basic task, you assign the time it takes to perform the task. You can build up a library of these basic tasks and then reuse them within your analysis.
In addition, you can define a task group, or multiple tasks performed together to complete a repair action, such as “replace motherboard”. For your systems, the steps required to replace the motherboard will be the same all the time – perhaps opening up a case, removing some screws or clips, swapping the board, and then closing the case back up. You can combine all those Maintenance Tasks into a single Maintenance Task Group to use in your analysis for quick and consistent measurement.
FD&I Outputs
FD&I Outputs, or Fault Detection and Isolation Outputs, are the activities performed in order to detect and isolate a failed item. Similar to Maintenance Task Groups, FD&I Outputs are typically defined as a group of tasks performed together as a unit.
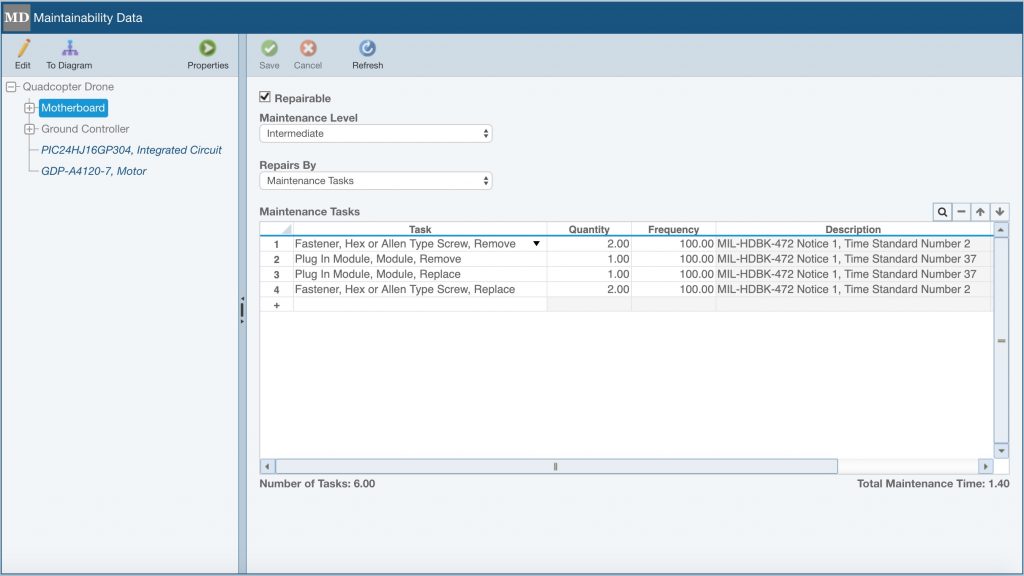
Relyence Maintainability Prediction allows you to define your maintenance activities by Tasks, Task Groups, or FD&I Outputs.
Maintenance Groups
Maintenance Groups define how a repair action is performed on a group of items, rather than on a single item. Some of the data required to define a Maintenance Group includes the repairable item access (single or multiple items), the replacement philosophy (group or iterative), and if reassembly of the unit is required for checkout.
Maintenance Tasks, Maintenance Task Groups, FD&I Outputs, and Maintenance Groups can be considered the building blocks for the Maintainability Prediction analysis. Once these are in place, you can then go step-by-step through the components in your system and describe the process and procedures required to repair and replace failed items.
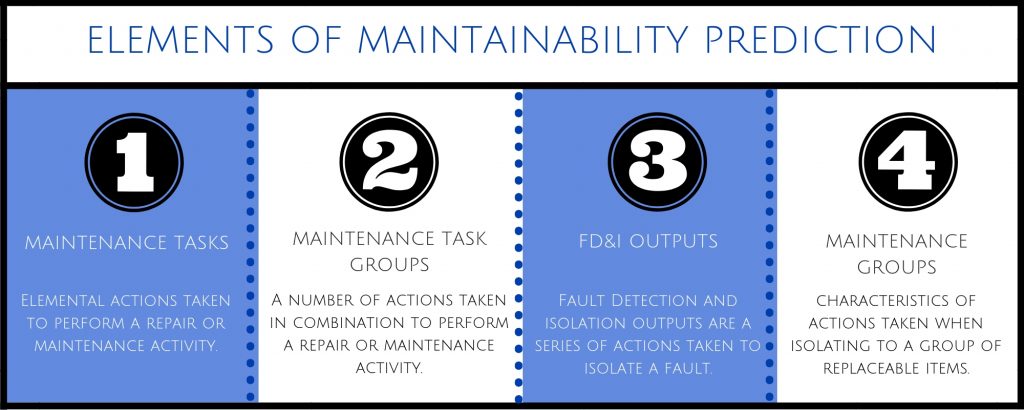
Four Elements of Maintainability Prediction
Maintenance Metrics
Once your maintenance activities are defined, you can then proceed to the central part of your analysis: computing maintenance metrics. Using MIL-HDBK-472 as a basis, you can calculate a host of metrics for assessment of your system’s repair statistics.
- MTTR: Mean Time to Repair
- MCMT: Mean Corrective Maintenance Time
- MPMT: Mean Preventive Maintenance Time
- MAMT: Mean Active Maintenance Time
- MMH/Repair: Mean Maintenance Hours per Repair
- MMH/MA: Mean Maintenance Hours per Maintenance Action
- MMH/FH: Mean Maintenance Hours per Flight Hour
- MMH/OH: Mean Maintenance Hours per Operating Hour
- Isolation to a Single RI: Percent isolation to a single replaceable item
- Isolation to a Group of RIs: Percent isolation to a group of replaceable items
- MaxCMT: Maximum Corrective Maintenance Time
- Maintainability Index
- Availability
- Individual MTTR Element Values: The summation of the results associated with Preparation, Fault Isolation, Disassembly, Interchange, Reassembly, Alignment, Checkout, and Start Up.
Relyence Maintainability Prediction
Relyence Maintainability Prediction is a browser-based, comprehensive package for performing Maintainability Prediction analysis. Fully implementing MIL-HDBK-472, Relyence Maintainability Prediction offers a host of features to help complete your Maintainability Prediction analyses accurately and efficiently.
Contact us today so we can talk about your MTTR software needs and how Relyence Maintainability Prediction can help, or sign up today for our free trial!