THE RELIABILITY PREDICTION STANDARDS
Supporting the most well-known and widely accepted reliability prediction standards – MIL-HDBK-217, Telcordia SR-332, 217Plus, NSWC Mechanical, ANSI/VITA 51.1, IEC 61709, China’s GJB/z 299 standards, as well as NPRD & EPRD – Relyence Reliability Prediction provides a fast and accurate tool for MTBF (Mean Time Between Failures) analysis.
Reliability prediction analysis enables you to assess and estimate the likely failure rate or MTBF of your product or system. By offering built-in support for all the worldwide accepted standards for analyzing the MTBF, Relyence Reliability Prediction computes the predicted MTBF of systems which incorporate a wide array of electronic and mechanical components. To learn more about which standard may be most beneficial for you, check out our blog post that delves into more details on the reliability prediction standards.
Whichever standard you select to use in our reliability prediction MTBF calculator tool, you can rest assured that Relyence Reliability Prediction fully implements all aspects of the model, such as failure rate adjustments based on test or field data, process grades, and cycling factors. We even go a step further – allowing you to mix prediction standards in your analyses – providing not just modeling flexibility, but ensuring you can most accurately evaluate your system reliability.
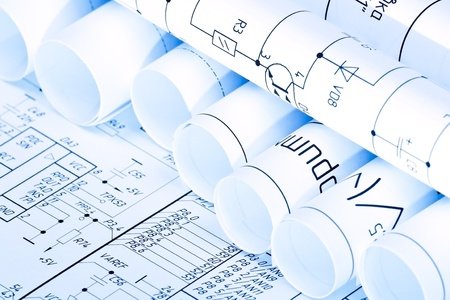
MIL-HDBK-217
Relyence Reliability Prediction supports the worldwide accepted handbook for prediction analysis – MIL-HDBK-217F Notice 2 (sometimes referred to as MIL-STD-217 and MIL-217). MIL-HDBK-217 defines the failure rate calculation models for the broadest range of electromechanical components, enabling you to effectively calculate and predict the failure rate and MTBF (Mean Time Between Failures) of your products. All facets of the standards are supported including full part stress calculations for all component types, parts count calculations, and hybrid modeling. Relyence Reliability Prediction makes it easy to move from your early design stage prediction based on parts count estimation to the fully detailed part stress analysis that can be performed later in the product development cycle when data parameters are known. Relyence Reliability Prediction can assume average default values for unknown parameters so that you can always perform MTBF assessments no matter how much data is available.
Telcordia SR-332
Relyence Reliability Prediction supports the most recent edition of the Telcordia standard: Telcordia SR-332 Issue 4 (also formerly known as the Bellcore standard). The Telcordia SR-332 standard includes models for a vast array of electromechanical devices. Telcordia uses a unique statistical approach to failure rate computations that involves means, standard deviations, and confidence levels. Unlike other prediction standards, the total failure rates computed using Telcordia are not equal to the summation of the underlying components’ failure rates. For an in-depth review of how Telcordia calculations are performed, see our informative blog post for an explanation.
Additionally, Telcordia incorporates methodologies for adjusting failure rates based on accumulated laboratory test results as well as collected actual field-based performance metrics. Telcordia also provides analysis techniques for calculating early life factors that can be utilized to evaluate early life failure rate. The advantage of using Relyence Reliability Prediction is that you can use these methodologies across any standard you are using to help refine your prediction analyses.
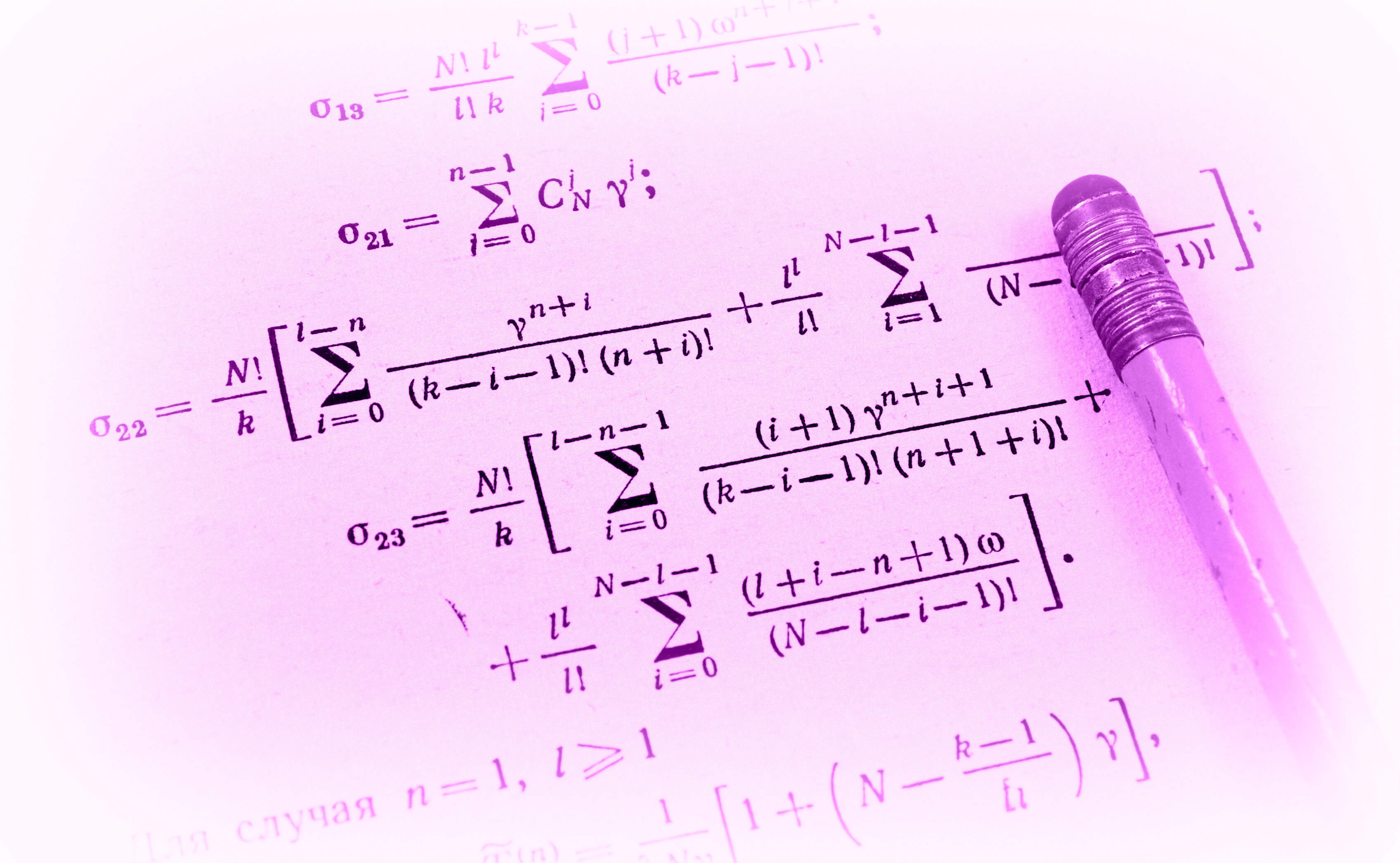
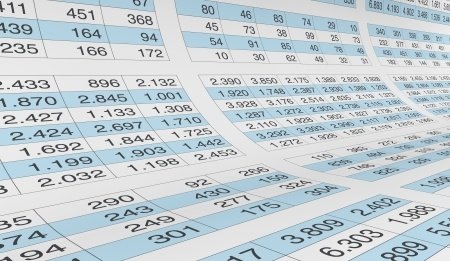
217Plus
The 217Plus™ reliability prediction standard, Handbook of 217Plus Reliability Prediction Models, was developed by Quanterion Solutions. Work on 217Plus was started under Department of Defense contracts with the Reliability Analysis Center (RAC) and Reliability Information Analysis Center (RIAC), and was released originally under the name PRISM. The failure rate models of 217Plus have their roots in MIL-HDBK-217, and include failure rate calculation models for a broad range of electromechanical components. All aspects of the standard are supported including detailed part stress calculations, parts count calculations, operating profiles, cycling factors, and process grades. Similar to MIL-HDBK-217, Relyence Reliability Prediction for 217Plus 2015 Notice 1 makes it easy to move from your parts count analysis in the early design stage to a fully detailed reliability prediction analysis performed later in the product development cycle when operating parameters are known.
NSWC Mechanical
Developed by the Naval Surface Warfare Center (NSWC), the NSWC-11 Handbook of Reliability Prediction Procedures for Mechanical Equipment details the reliability prediction procedures for a variety of mechanical parts. The standard includes models to compute the failure rate of various mechanical components such as gears, springs, pumps, gaskets, and many more.
Because operating conditions can vary across applications, the NSWC-11 models take operating conditions and material properties into account for failure rate calculations. The appropriate factors vary depending on the part being modeled but can include aspects like misalignment, loading factors, viscosity, and material hardness.
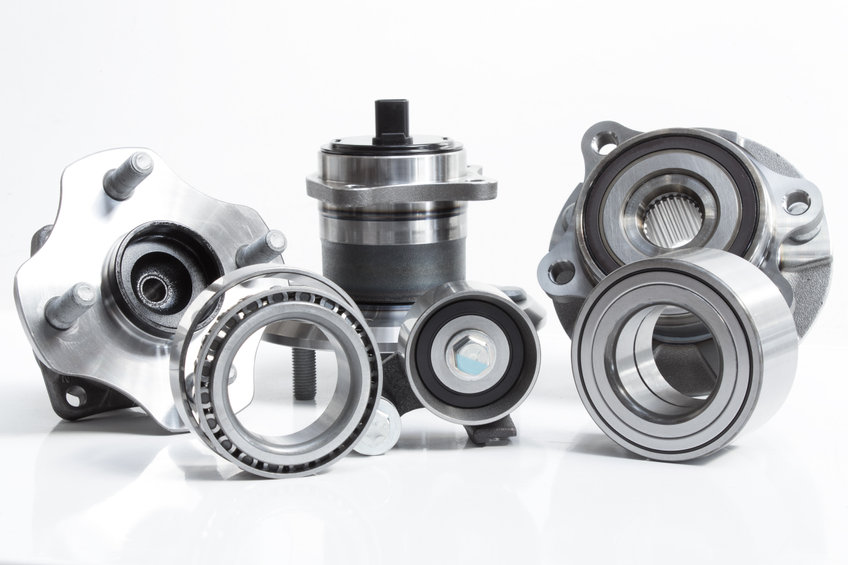
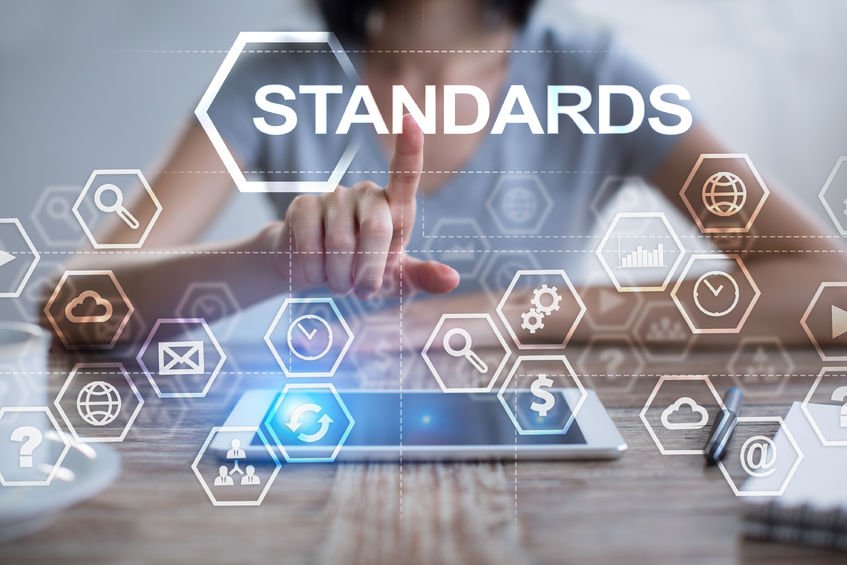
ANSI/VITA 51.1
Relyence Reliability Prediction offers the ability to perform your reliability predictions using the ANSI/VITA 51.1 recommended updates to MIL-HDBK-217 F Notice 2.
ANSI/VITA 51.1 is a collaborative industry standard that provides recommended modifications to the MIL-HDBK-217 F Notice 2 Reliability Prediction Handbook to reflect more updated failure rate assessments. The ANSI/VITA 51.1 rules, recommendations, and suggestions take into account changes in device technologies, improvements that have occurred over time since the MIL-HDBK-217 F Notice 2 standard was released, and updated data parameters to more accurately model current device quality and performance.
NPRD and EPRD
Relyence Reliability Prediction supports both the NPRD (Non-electronic Parts Reliability Data) and EPRD (Electronic Parts Reliability Data) databases. NPRD and EPRD include a wide array of devices that you can use to expand your predictions beyond the components modeled in the standards. Taking advantage of this powerful add-on enables your predictions to more accurately reflect your system design. The NPRD and EPRD publications include a library of components and their representative failure data. The data is extensive and represents a wide variety of devices and sources. Adding these components into your reliability prediction analyses allows you to build a complete system model and more accurately assess your product reliability.
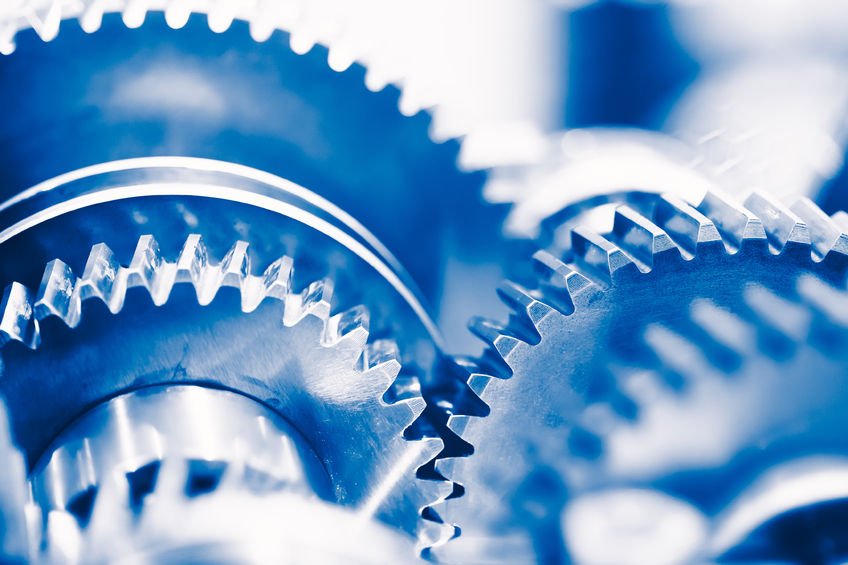
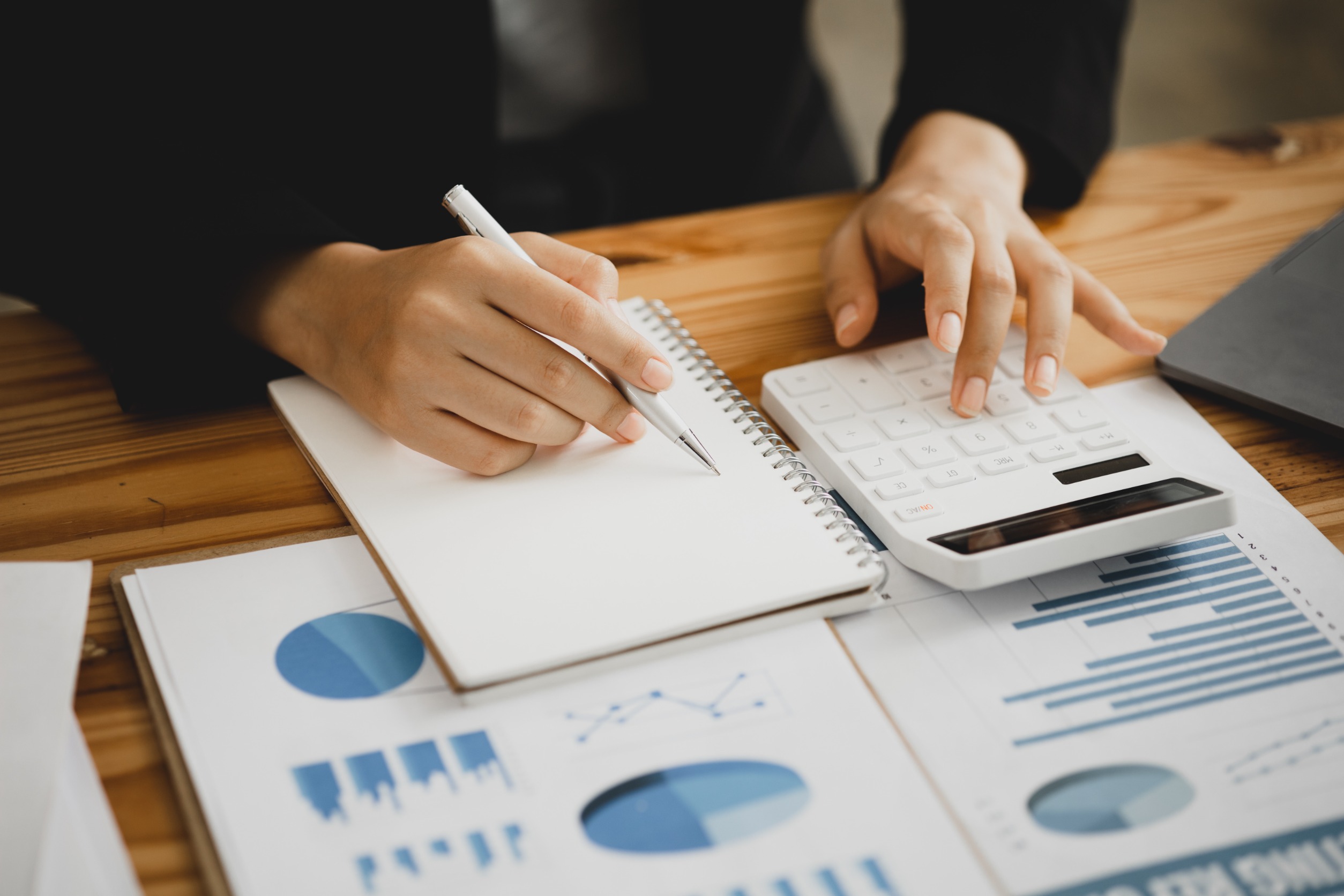
IEC 61709
The IEC 61709 standard, entitled “Electric components – Reliability – Reference conditions for failure rates and stress models for conversion” was developed by the International Electrotechnical Commission (IEC). It provides stress models to convert failure rates from reference conditions to different operating conditions for a variety of electromechanical components. By providing a conversion model between differing conditions, the methods presented in IEC 61709 provide modified failure rate values based on the effects of variations in the design or environment.
Relyence supports the use of IEC 61709 failure rate conversions in conjunction with other supported reliability prediction standards. This allows you to use a standard such as MIL-HDBK-217 to compute a failure rate to use as the reference value for IEC 61709 failure rate calculations.
China’s GJB/z 299
Relyence Reliability Prediction provides support for the prediction standard with one of the largest international user bases: GJB/z 299C from China. Similar to MIL-HDBK-217 in breadth and depth, the Chinese GJB/z 299C prediction standard supports a wide range of electromechanical components, a large selection of environments, part stress calculations, parts count calculations, and the ability to model foreign manufactured devices. Because Relyence is available in a Chinese translated version, China’s GJB/z 299C can be used fully in Chinese and can be accessed in a hosted version in China.
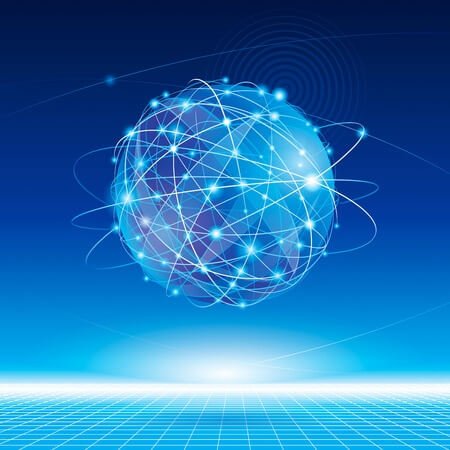
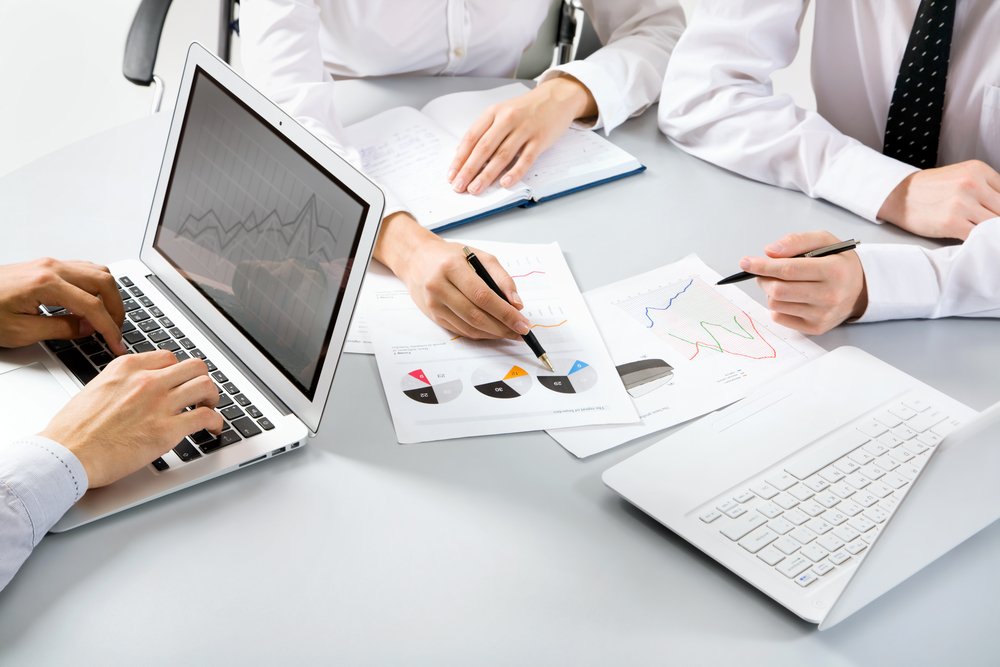
Mixed Modeling
Relyence Reliability Prediction enables you to access the features and functions of the prediction standards across all models. For example, if you are performing a MIL-HDBK-217 analysis, but would like to adjust your failure analysis based on laboratory test data you have acquired, you can do this using the laboratory test adjustment techniques defined in the Telcordia standard. Or, if you are performing a Telcordia analysis, but have a component not modeled in Telcordia, but available in MIL-HDBK-217, simply specify that component as a MIL-HDBK-217 part and Relyence will automatically access the appropriate failure rate model. The ability to mix model capabilities allows your prediction analyses to be accurate, effective, and most reflective of actual system performance.