Maintainability is an important aspect in system continuous improvement efforts. The term maintainability is used to denote how a system or product is kept in operating order so that it continues to achieve its performance objectives. A maintainability program may include procedures that are corrective or preventive in nature. Corrective maintenance tasks involve making repairs upon component failures, while preventive procedures are put in place to keep systems from failing.
Maintainability of any product or system is critical because it directly impacts system availability. Accordingly, an important part of assessing uptime, or availability, includes the evaluation of your repair and maintenance times. For example, if a system fails but can be repaired quickly, system uptime remains high. System uptime and downtime are key measures that impact business success. In some industry sectors, such as in aerospace, defense, telecommunications, manufacturing, and other vital service sectors, system downtime is a crucial measure.
What is Maintainability Prediction?
Maintainability Prediction provides a way to analyze a system to determine repair and maintenance metrics that affect system availability. MTTR (Mean Time to Repair), MCMT (Mean Corrective Maintenance Time), and MPMT (Mean Preventive Maintenance Time) are some of the values computed by Maintainability Prediction analysis.
MIL-HDBK-472 provides a well-accepted and proven methodology for assessing maintainability metrics. It includes mathematical equations used to estimate key maintainability and repair related measures. The calculations are based on the maintenance tasks or FD&I (Fault Detection & Isolation) Outputs needed to complete a maintenance activity and their associated times.
One of the main advantages of maintainability predictions is that they can be performed during the product design stage, enabling you to preview likely maintainability metrics. You can use this information to optimize your maintenance and repair activities to keep your system up and running with minimal downtime.
This article describes Maintainability Prediction analysis based on the techniques described in MIL-HDBK-472 using Relyence Maintainability Prediction.
What are the Elements of Maintainability Prediction?
There are several elements that form the basis to begin an analysis using MIL-HDBK-472: Maintenance Tasks, FD&I Outputs, and Maintenance Groups.
Maintenance Tasks
Maintenance Tasks represent any individual step taken to repair or perform maintenance on an item. When specifying a Maintenance Task, you define the following characteristics:
- Maintenance Type: Indicates if the Task is associated with a Corrective, Preventive, or False Alarm action. Corrective Tasks are done when repairing or fixing a failed item. Preventive Tasks are maintenance actions that are performed to keep an item in operating condition and are typically scheduled to be completed at certain intervals. False Alarm Tasks are performed when a false alarm occurs.
- Preventive Frequency: Enter the frequency if the Task is a preventive measure. In Relyence Maintainability Prediction, enter the frequency in your failure rate units. For example, if your failure rate unit setting is FPMH (Failures per Million Hours), enter the frequency in units of actions per million hours.
- Maintenance Time: The time the Task takes, in minutes.
- Number of Persons: The number of people performing the Task.
- MTTR Element: This is an indication of which phase of repair the Task is associated with. As defined in MIL-HDBK-472, the choices are: Preparation, Fault Isolation, Disassembly, Interchange, Reassembly, Alignment, Checkout, and Start Up. If entered, this allows you to compute MTTR values for each of these stages individually. This can help you zero in on the maintenance area that takes the most time. For example, if you see that “Reassembly” is the main driver of a high MTTR, you can focus activities to find ways to improve the reassembly procedure or modify the design to make it easier to reassemble after repair.
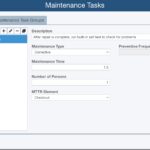
Maintenance Tasks can include details such as Maintenance Type, Maintenance Time, Number of Persons, and MTTR Element.
Maintenance Task Groups
Maintenance Task Groups allow you to combine a series of tasks that are performed together into a single element. This is useful for sets of tasks that are commonly performed as a group and makes data entry easier. For example, the initial steps of a disassembly process may be to turn the power off, remove two screws, unplug a connector, and remove a PCB. In this case, these 4 tasks can be defined in a single Task Group which can then be easily reused throughout your Maintainability Prediction analysis.
For Maintenance Task Groups, you select the Maintenance Type, either Corrective, Preventive (along with Frequency), or False Alarm. You then list out the tasks that are included for the Group. With each Task, you can define a Quantity for cases where a single Task is performed more than one time.
FD&I Outputs
Fault Detection and Isolation (FD&I) Outputs are tasks performed in order to detect and isolate the source of failure. For example, a subsystem may arrive for repair and it may be necessary to find which component within the subsystem failed. When defining FD&I Output tasks, the following information is needed:
- Quantity: The number of times the Task is performed during the maintenance action. For example, a “2” would indicate you have to do that Task twice, such as replacing two screws.
- Frequency: The frequency of occurrence of the Task expressed as a percentage from 0 to 100 to indicate how often that Task is performed as part of the FD&I. For example, some lower-level tasks may not need to be performed if the source of the failure had been found prior to performing the task.
Maintenance Groups
MIL-HDBK-472 describes more than one method for calculations: Procedure 2, Procedure 5 Method A, and Procedure 5 Method B. Maintenance Groups are only necessary if you choose to perform Procedure 5A calculations. The data required for Maintenance Groups includes:
- Repairable Items Access: This indicates the complexity of making the repair – a choice of Single or Multiple. Single indicates that the individual item under repair is directly accessible. If more than a single item needs to be removed in order to complete the task, Multiple should be selected.
- Replacement Philosophy: An indication of how item replacement is accomplished – a choice of either Group or Iterative. Group indicates that an entire group of items will be replaced during a repair. Iterative indicates that a single item is replaced at a time until the malfunctioning item is isolated.
- Reassembly required for checkout: This applies to Iterative Replacement only. It indicates if the system must be reassembled in order to verify that the repair is successful.
- Average number of repairable items per iteration for fault: This is a numerical estimation of the number of repairable items involved during each iteration on average. MIL-HDBK-472 provides details on various ways to assess this value.
Entering Maintainability Data
Once the building blocks for your Maintainability Prediction are defined, you can then proceed to enter the repair and maintenance activity data for the items in your system.
Understanding Maintenance Levels
One of the first items to define is the Maintenance Level for each repairable item. The Maintenance Level indicates where the maintenance or repair is completed. The 3 choices, as defined in MIL-HDBK-470A and referenced in MIL-HDBK-472, are:
- Depot: This indicates the action is performed at a highly specialized repair facility, typically not the location where the system is currently located. When Depot is selected it is usually an indication that the system is undergoing a significant maintenance operation, such as a major update or rebuild.
- Intermediate: The maintenance is performed at a designated location such as an onsite repair or maintenance facilities, or by designated maintenance personnel.
- Organizational: The repair is done at the operating site and can be done by personnel without specialized training.
In Relyence Maintainability Prediction, the Maintenance Levels use the MIL-HDBK-472 choices as a default, however, you can customize the Maintenance Levels to your preferences.
Entering Maintenance and Repair Procedures
The information needed for your repairable items includes:
- Repairable: First you must indicate that the item is repairable. In some cases, elements of your system may not be repairable, so data about the repair process is unnecessary.
- Maintenance Level: An indication of where the repair is done. Default choices are set to Depot, Intermediate, or Organizational. However, you can modify these if desired.
- Maintenance Group: If you are using MIL-HDBK-472 Procedure 5, Method A, then the associated Maintenance Group must be selected.
- Repairs by: If you are defining the process using Tasks, select Maintenance Tasks. Otherwise, select FD&I Outputs.
- Table of Maintenance Tasks or FD&I Outputs: Select all the Tasks or FD&I Outputs that are performed for the repair of the system component. For each Task, enter the Quantity and Frequency.
When Maintenance Tasks or FDI& Outputs are selected in Relyence Maintainability Prediction, you will see the associated data for each Task or FD&I Output in the Table. The Maintenance Time for each line item factors in the defined Maintenance Task Quantity. At the bottom of the table, you will see the total Number of Tasks and the Total Maintenance Time. For FD&I Outputs, the Total Percent is shown so you can ensure your percentages add up to the appropriate 100% total.
Data entry of Tasks and FD&I Outputs is also made easier in Relyence using the Search Bar in the dropdown lists. You can type in any text and the list will be filtered to show only the matching choices. For example, if you are looking for a Task related to “wirewrap”, simply type in “wirewrap” in the Search Bar and the list will only show the items pertaining to connector related Tasks or FD&I Outputs.
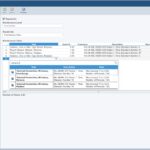
Use the Maintenance Tasks Table to define the repair or maintenance activities for your components.
Maintainability Prediction Calculations
Repair metrics are the central element of Maintainability Prediction. These metrics provide insight to help you control your maintenance activities and achieve system performance goals.
Maintainability Prediction Properties
There are a few settings to help establish how to perform calculations. In Relyence Maintainability Prediction, these are found under Properties, accessed from the Relyence Sidebar menu.
The settings include:
- False Alarms Frequency: Set the frequency of both Type 1 and Type 2 False Alarms. Type 1 False Alarms are detected during normal operation but cannot be reproduced during the fault isolation process. Type 2 false alarms are detected and isolated, but the item does not have an actual fault.
- Maintenance Time Adjustment: This enables you to globally adjust your maintenance times. The choices are:
- None: This is the default setting and means that all maintenance times are set from your data entry tables.
- Add: Repair times are adjusted by adding the Value entered.
- Multiply: Repair times are adjusted by multiplying by the Value entered.
- Procedure 5, Method A: Indicates if Procedure 5, Method A calculations according to MIL-HDBK-472 are to be used. In general, Procedure 5A calculations are used when predicting maintainability measures of avionics, ground, and shipboard electronics in early design stages. However, it is not limited to those areas, and can be useful in any environment and all types of equipment, including mechanical systems. It provides itemized maintainability metrics based on Replacement Philosophy and Maintenance Groups.
Maintainability Prediction Metrics
Maintainability Prediction analyzes an array of metrics. Depending upon your requirements, you can choose which measures are needed.
MTTR (Mean Time to Repair)
The classic repair metric, MTTR is the average time to it takes to repair a failed unit and return it to an operational state. It is calculated for all replaceable items by the following equation:
MTTR = Σ (Corrective Repair Times * Failure Rate) / Σ Failure Rates of items at specified Maintenance Level
MCMT (Mean Corrective Maintenance Time)
MCMT represents the mean time required to perform all corrective maintenance actions necessary to return a failed system back to operation status. Corrective maintenance includes the repair or replacement of failed components.
MPMT (Mean Preventive Maintenance Time)
MPMT is the mean time required to perform all preventive maintenance actions. These are the actions taken to help prevent the failure of components in order keep a system in an operational state.
MAMT (Mean Active Maintenance Time)
MAMT is the average time required to perform all corrective and preventive maintenance actions.
Maintainability Index
Maintainability Index is the total maintenance effort, including both preventative and corrective maintenance, that is required to maintain a product so that it remains operational during a specific time period. It is based on the MAMT calculation as well as the calendar time in operating inventory (Tj), the operating time during Tj (Ti), and the operating time (T). All units for these times are in hours.
Availability
Availability is the probability that an item is operating at a specific point in time. It is based on both MTBF (Mean Time Between Failure) and MTTR (Mean Time To Repair). Oftentimes, MTBF values are obtained from a Reliability Prediction analysis on the system, otherwise, they must be manually entered.
MTTR Elements Summation
MTTR Elements Summation will compute the hours spent in each of the MTTR Elements as defined in MIL-HDBK-472: Preparation, Fault Isolation, Disassembly, Interchange, Reassembly, Alignment, Checkout, and Start Up.
MMH/Repair (Mean Maintenance Hours per Repair)
MMH/Repair is similar to MTTR, except manhours are used instead of repair times. It is the average number of manhours to repair or maintain an item. It does not take into account Preventive Tasks or False Alarms.
MMH/MA (Mean Maintenance Hours per Maintenance Action)
MMH/MA is similar to MMH/Repair but takes into account time spent from False Alarms.
MMH/FH (Mean Maintenance Hours / Flight Hours)
MMH/FH is the sum of all corrective, preventive, and false alarm times divided by total flight hours. To compute flight hours, enter the Percentage Flight Hours in reference to total operating hours.
MMH/OH (Mean Maintenance Hours per Operating Hour)
MMH/OH is the sum of all corrective, preventive, and false alarm times divided by total operating hours.
Isolation to a Single RI (Isolation to a Single Replaceable Item)
Isolation to a Single RI is the percentage of faults detected that can be isolated to a single component or replaceable item.
Isolation to a Group of RIs (Isolation to a Group of Replaceable Items)
Isolation to a Group of RIs is the percentage of faults detected that can be isolated to the specified Quantity, or fewer, replaceable items. For example, if Quantity is set to 3, the result will show the percentage of faults detected that can be isolated to 3 or fewer replaceable items.
MaxCMT (Maximum Corrective Maintenance Time for Sigma percentile)
MaxCMT is the time needed to accomplish the specified percentage of potential corrective maintenance tasks. Enter the Percentile to use for the MaxMCT. The 90th or 95th percentiles are commonly used, which indicate the time within which 90% or 95% of maintenance actions can be completed.
Example Maintainability Prediction Calculation
For a sample case, we will use the Quadcopter Drone Example from Relyence. We obtain failure rate data using Relyence Reliability Prediction for use in our Maintainability Prediction calculations.
Step 1: Define Analysis Tree and Perform Reliability Prediction Analysis
Our example Drone includes two main subsystems: a Motherboard with built-in GPS and a Ground Controller unit. Our Reliability Prediction analysis provides the following results:
Step 2: Enter Repair Information
Then, we can enter repair tasks for any or all elements in our Analysis Tree. For this example, we will assume the Motherboard and the Ground Controller are repairable. We then move to Maintainability Prediction and enter the repair tasks required for the Motherboard and Ground Controller subsystems.
Step 3: Obtain Repair Metrics
Next, we are going to calculate the repair metrics MTTR, MCMT, MMH/MA, and Availability. Because we are obtaining failure rate values from Reliability Prediction, we make sure that our results are up to date by selecting the Calculate Reliability Prediction before calculating Maintainability Prediction checkbox.
The results are shown in the calculation results dialog. We can click on each item in the Analysis Tree to view its corresponding repair metrics. Additionally, for this simple example, we can analyze the MTTR calculations for each Analysis Tree item by using the equation below:
MTTR = Σ (Corrective Repair Times * Failure Rate) / Σ Failure Rates of items at specified Maintenance Level
Note that all values are expressed in units of Hours.
Motherboard:
Corrective Repair Time = 1.4 minutes = 0.023333 Hours
Failure Rate = 22.466950 FPMH = 22.466950 e-6 Failures/Hour
MTTR = (0.023333 * 22.466950 e-6) / 22.466950 e-6= 0.023333 Hours
Ground Controller:
Corrective Repair Time = 0.29 minutes = 0.004833 Hours
Failure Rate = 0.4251114 FPMH = 0.4251114 e-6 Failures/Hour
MTTR = (0.004833 * 0.425114 e-6) /0.425114 e-6 = 0.004833 Hours
Quadcopter Drone:
The Quadcopter Drone MTTR is calculated from a roll up of lower-level Motherboard and Ground Controller metrics.
Σ (Corrective Repair Times * Failure Rate) = (0.023333 * 22.466950 e-6) + (0.004833 * 0.425114 e-6) = 0.5262758 e-6
Σ (Failure Rates at Intermediate Level) = 22.466950 e-6 + 0.425114 e-6 = 22.892064 e-6
MTTR = 0.5262758 e-6 / 22.892064 e-6 = 0.02299 Hours
MTTR Calculations by Maintenance Level
In this example, we have all Maintenance Levels set to Intermediate, so only MTTR values at the Intermediate Level will be computed. Maintainability Prediction metrics are calculated at each Maintenance Level independently. When multiple Maintenance Levels are defined, only the values associated with each Level are used in the calculations. For this example, we selected “Intermediate” for the MTTR calculation, so the analytical engine is only factoring in items set to Intermediate. In this case, that happens to be all the Tasks. However, if this example included any Depot or Organizational Level Tasks, they would not be taken into account for the MTTR result at the Intermediate Level.
If you prefer, you can compute results at all defined Maintenance Levels. The underlying equations remain the same, but the items taken into account are filtered by Maintenance Level.
Other Repair Metrics
In this example, MCMT (Mean Corrective Maintenance Time) is equal to MTTR because all our Tasks are Corrective. You can also see that the overall Availability of our Quadcopter Drone is very high due to the low failure rates and quick repair times.
Relyence Maintainability Prediction
The best-in-class Relyence Maintainability Prediction is a complete and accurate software tool for performing your MIL-HDBK-472 maintainability analyses. It offers a host of features to make your Maintainability Predictions quick and efficient, including all the functions and features outlined in this article. Relyence Maintainability Prediction provides a solid foundation for all your maintenance and repair analysis needs and adds a key element to your reliability and quality analysis tool set.
Contact us today so we can talk about your Maintainability Prediction needs, or sign up today for our free trial to see Relyence Maintainability Prediction in action, or schedule a personalized demo at a time convenient for you.