We are excited to announce the release of Relyence 2025 Release 1, packed with an array of innovative new features and enhancements. This latest release reflects our commitment to staying at the forefront of industry advancements with key additions in Relyence FMEA, Reliability Prediction, FRACAS, and RBD. Discover more about this exciting new release by reading further or check out our highlights video for a concise overview.
Introducing FMEA Function and Failure Nets
Relyence FMEA is designed to streamline and enhance Failure Mode and Effects Analysis across a wide range of industries, including automotive, aerospace, electronics, medical devices, and more. Already known for our intuitive and advanced capabilities such as the FMEA Knowledge Bank, Relyence 2025 Release 1 continues to propel our best-in-class FMEA tool even further with the introduction of FMEA Function and Failure Nets. This powerful enhancement builds upon traditional Failure Mode and Effects Analysis by offering a dynamic, visual representation of your FMEA data including Functions, Failure Modes, and their associated Causes and Effects across your system structure.
What are the benefits of using FMEA Nets?
Often used prior to building your Worksheets, FMEA Nets offer a visual view of your system’s FMEA data and provide a few key benefits to the FMEA process.
- Enhanced Visualization: The graphical format provided by FMEA Nets gives an intuitive and easy-to-understand view into your FMEA data and the relationships between system elements, their Functions, and Failure Modes. This enables your entire team to understand your systems’ interactions and allows for more complete analyses.
- Intuitive Traceability: FMEA Nets allow you to gain an understanding of failure chains and easily trace the propagation of failures across your system. This aids in identifying high-impact areas for risk reduction.
- Comprehensive Data Capture: By providing an intuitive way to see the interconnections between higher and lower level FMEA data, FMEA Nets ensure all appropriate FMEA data is captured for each system component. This ensures your failure modes and effects analyses are complete and comprehensive.
- Efficient Worksheet Building: FMEA Nets in Relyence FMEA allow you to add Functions, Failure Modes, Causes, and Effects directly to your DFMEA Worksheet, providing you with a helpful starting place for efficient Worksheet completion.
By providing a helpful visual representation of your FMEA data, FMEA Nets offer a valuable tool to improve the FMEA process, making it easier to pinpoint vulnerabilities and implement effective risk mitigation strategies.
Function Nets
Function Nets in FMEA are a way to represent the relationships visually and logically between the Functions within a system. They map out how your system’s Functions interconnect and depend on one another, allowing for a clearer understanding of the overall system functionality and its potential vulnerabilities. Using Function Nets can enable a better understanding of how the failure of one Function can impact others, leading to more accurate identification of failure modes, causes, and effects.
In a Function Net, each block represents a specific Function, and the links between blocks indicate dependencies or interactions to Functions at higher and lower levels of your system in the Analysis Tree. In Relyence FMEA, Focus Function denotes the Function that is currently under examination and is selectable from the dropdown menu in the Focus Failure pane. Or, you can also add a new Focus Function for analysis from the Sidebar. From your Focus Function, you can then efficiently build your Function Nets by using the Next Higher Level and Next Lower Level Sidebar tools to add Functions. As Function data is connected or added from the Function Net, it is then automatically added to the DFMEA Worksheet.
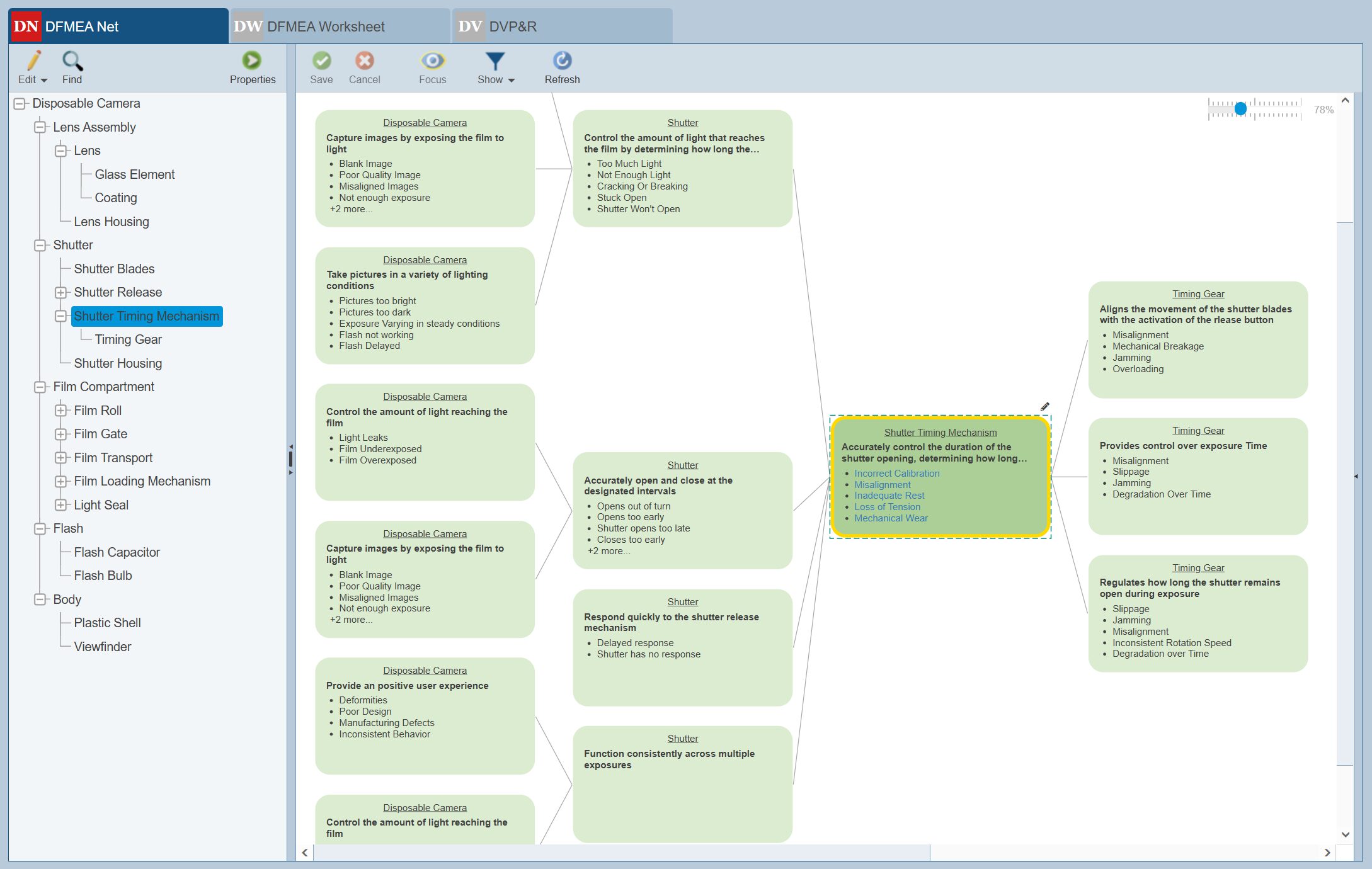
Function Nets in DFMEA map out how your system’s Functions interconnect and depend on one another.
Function Nets are a powerful tool for your Design FMEAs, offering a structured way to explore and analyze the interplay between system Functions and can help uncover design weaknesses and opportunities for improvement.
Failure Nets
Failure Nets in FMEA provide a structured approach to visualizing and analyzing how failures propagate through a system. Similar to Function Nets but with an emphasis on system failures instead of Functions, they focus on the relationships between Failure Modes at different levels of your system’s Analysis Tree. Using Failure Nets can enable a deeper understanding of potential system weaknesses and interdependencies. One particular advantage offered by Failure Nets is the ability show how a single lower-level Failure Mode can lead to multiple Failure Modes or cascading effects, making it easier to analyze failure propagation. By understanding which failure causes or modes have the greatest downstream impact, you can prioritize mitigation efforts where they will have the most significant impact.
Each block in a Failure Net represents a specific Failure Mode with the links between blocks indicating the interactions to higher and lower-level Failure Modes. Similar to Function Nets, Focus Failure is used to denote the Failure Mode currently being analyzed and your Failure Net can be built using the Next Higher Level and Next Lower Level sidebar tools. To provide more context to your Failure Net, you have the option to show the Function associated with each Failure Mode on the appropriate block. Additionally, you can choose to show DFMEA Worksheet Causes and Effects on the Focus Failure block if desired. With this option turned on, you can then easily add higher-level Failure Modes as Effects and lower-level Failure Modes as Causes to your current Focus Failure. As Failure Mode, Cause, and Effect data is connected or added to your Function Net, it is then automatically added to the DFMEA Worksheet.
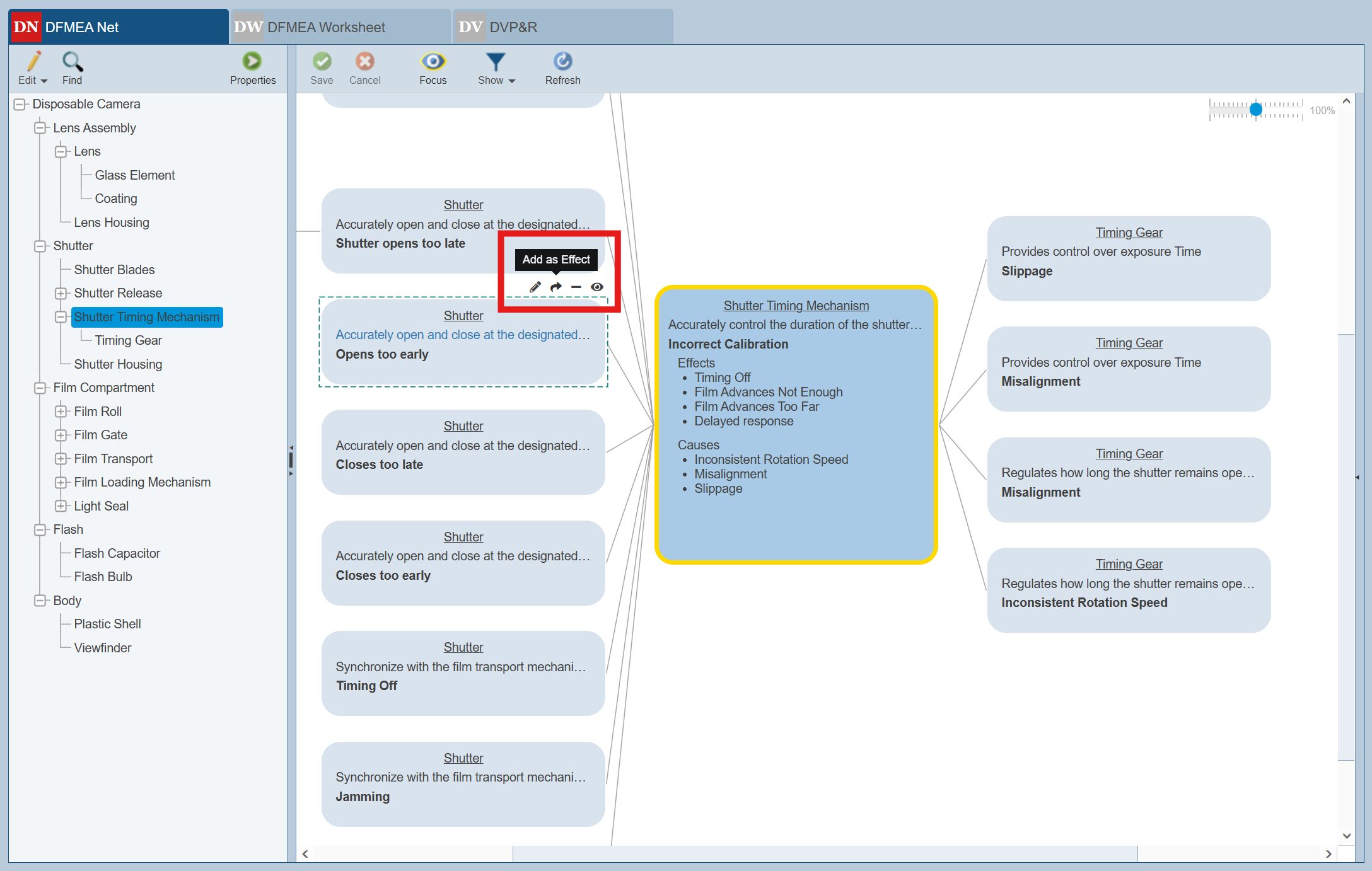
Failure Nets in Relyence FMEA provide a visual representation of the Failure Modes in your system and easily allow you to add Causes and Effects to your Focus Failure.
Failure Nets provide a clear visualization of how failures can cascade through a system, helping identify critical failure paths that may not be as obvious in a linear FMEA Worksheet.
FMEA Nets in Relyence
Support for Function and Failure Nets is available for your Design FMEAs. With this new exciting addition, we have included some helpful features that ensure you are getting the most out of your FMEA Nets:
- The Focus button in the toolbar and on blocks allows you to easily navigate through your Nets
- Hyperlinks on blocks link directly to the appropriate Function or Failure Net allow for quick navigation between functional analysis and failure analysis
- Function and Failure Mode text is easily edited directly on the appropriate Focus item
- The ability to filter on Subsystems and Functions provides a concise list of higher and lower-level data
Support for EPRD 2024 in Reliability Prediction
Relyence Reliability Prediction is a comprehensive tool designed to analyze and predict the reliability of systems and components using industry-standard methodologies, such as MIL-HDBK-217, Telcordia, and NSWC-11. With its intuitive interface and powerful analytical capabilities, Relyence Reliability Prediction helps organizations improve product reliability, optimize designs, and meet compliance requirements effectively.
Relyence 2025 Release 1 now includes the ability to add-on optional support for the latest version of the Electronic Parts Reliability Data database, EPRD 2024. This updated database provides comprehensive statistical information on failure rates and life expectancy for a broad spectrum of electronic components, including resistors, capacitors, semiconductors, and other commonly used parts across various industries. With its extensive catalog, EPRD 2024 ensures wide-ranging coverage of components and sources, making it a valuable resource for reliability analysis.
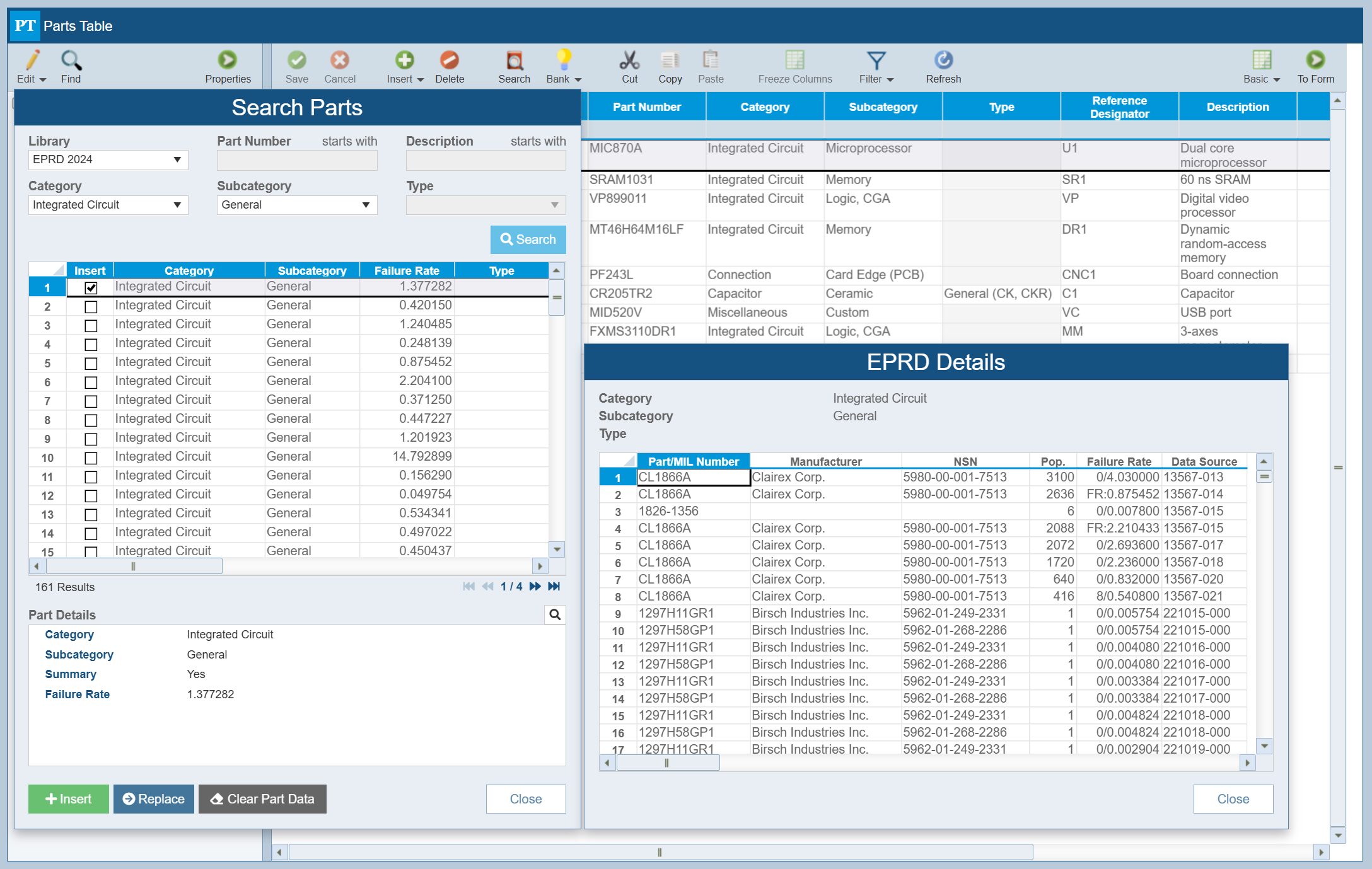
Relyence 2025 Release 1 now includes the ability to add-on optional support for EPRD 2024.
EPRD enables analysts to determine failure rates for electronic components that may not be covered by traditional calculation standards like MIL-HDBK-217. This capability ensures a more accurate and complete calculation of a system’s overall failure rate by incorporating all its elements. By offering detailed component data beyond standard models, EPRD enhances the precision and reliability of your predictions. For example, if you are using MIL-HDBK-217 for your failure rate calculations but encounter a specific type of integrated circuit not covered in the standard, you can consult the EPRD 2024 database to determine if EPRD 2024 may include failure rate models for that particular component. Relyence Reliability Prediction allows you to review all relevant EPRD Details from the EPRD Details Lookup, including data sources and references, ensuring you can make informed decisions when adding the component to your analysis. Once integrated, the system MTBF calculations will incorporate EPRD 2024 data, delivering a more accurate and comprehensive reliability assessment.
Enhanced Incident-Problem Integration in FRACAS
Relyence FRACAS is a powerful platform for managing corrective actions, ensuring your processes remain compliant and under control. It offers out-of-the-box support for various methodologies, including 1-step and 3-step Incident Management, 8D Problem Solving, the DMAIC Improvement Cycle, and the PDCA (Deming) Cycle, enabling you to get started quickly and efficiently. You can utilize these built-in templates as they are or leverage the platform’s customization capabilities to adapt Relyence FRACAS to meet the specific needs of your process.
In FRACAS, an Incident refers to a specific failure or unexpected event that occurs during the operation of a system while a Problem is a recurring or systemic issue that is often identified through the analysis of multiple Incidents. Problems frequently require investigation and corrective action to prevent future occurrences. Building on the robust capabilities of Relyence FRACAS, we’ve introduced new features that strengthen the relationship between Incidents and Problems.
Table view on Associated Incidents and Problems
Now in Relyence 2025 Release 1, you have the option to show the Associated Incidents or Problems data in a Subtable view on your FRACAS Forms. This new feature allows you to show the appropriate fields for the Associated items directly on your FRACAS Forms. This streamlines your corrective action process by reducing the need to switch between Incidents and Problems, enabling you to see both at one time.
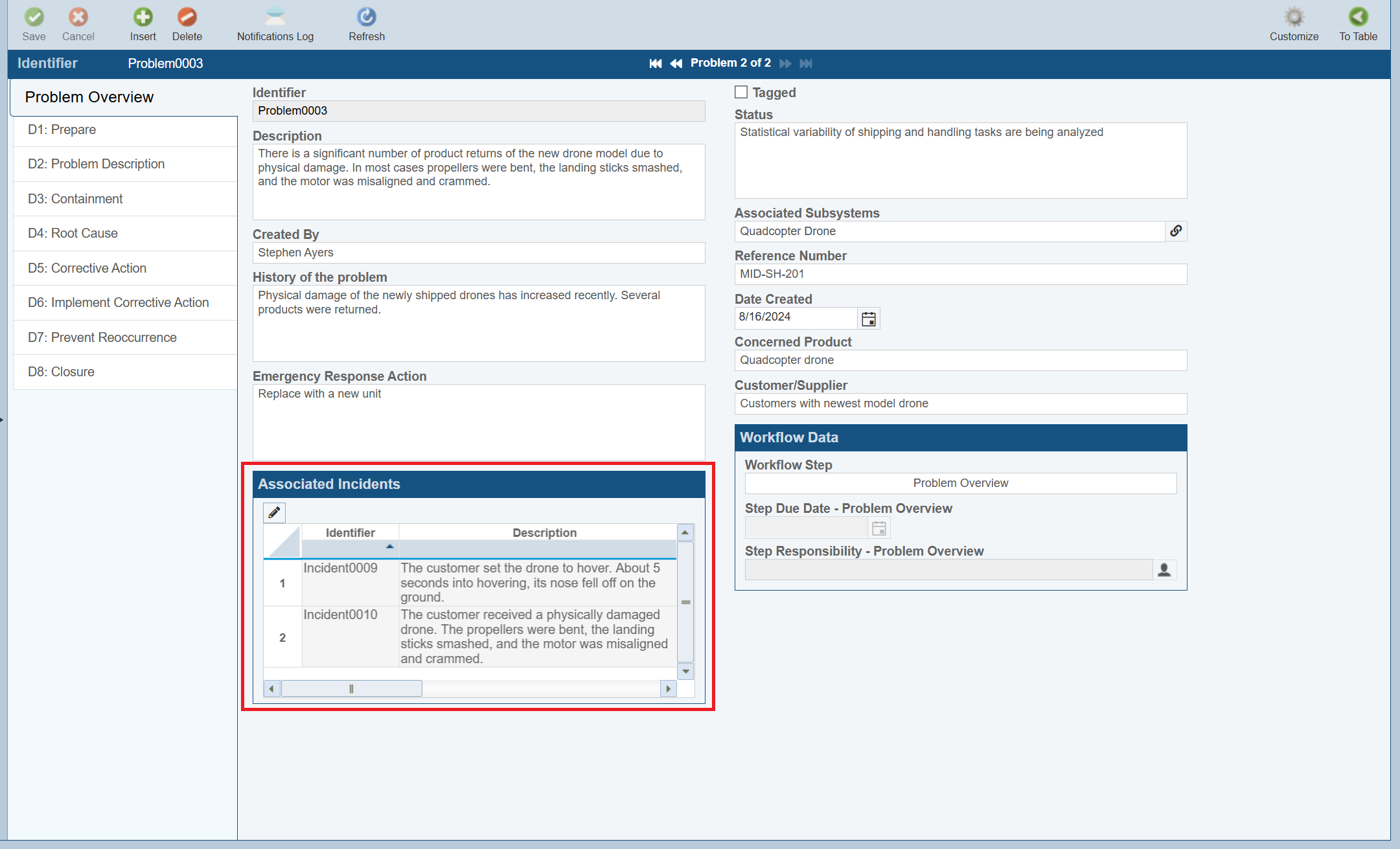
You have the option to show the Associated Incidents or Problems data in a Subtable view on your FRACAS Forms.
To see Associated items as a Subtable view in Relyence FRACAS, navigate to Customize from your Incident or Problem Form, select the appropriate Associated field and select the Show Associations as a Subtable option from the Edit Field dialog.
Additional Formula Capabilities
Using custom Formulas in Relyence FRACAS allows you to tailor the platform to meet your specific organizational needs and enhance its functionality. Custom Formulas empower you to maximize the potential of Relyence FRACAS, making it a more effective tool for tracking, analyzing, and resolving incidents and problems within your organization.
Now with Relyence 2025 Release 1, you have the ability to use your Incident fields in Problem calculations and vice versa. This new enhancement strengthens the already powerful capabilities that are available in FRACAS Formula creation to tailor the corrective action process to your organization’s needs. Some example calculations that this new capability provides include:
- Sum up the Repair Cost for all Incidents associated with a given Problem
- Determine the Average Time To Close for all Incidents associated with a given Problem
- On Incident Entry, automatically populate the Mitigation Steps previously taken from a completed Associated Problem
- Set the Issue First Discovered Date on a Problem from the earliest date from all Associated Incidents
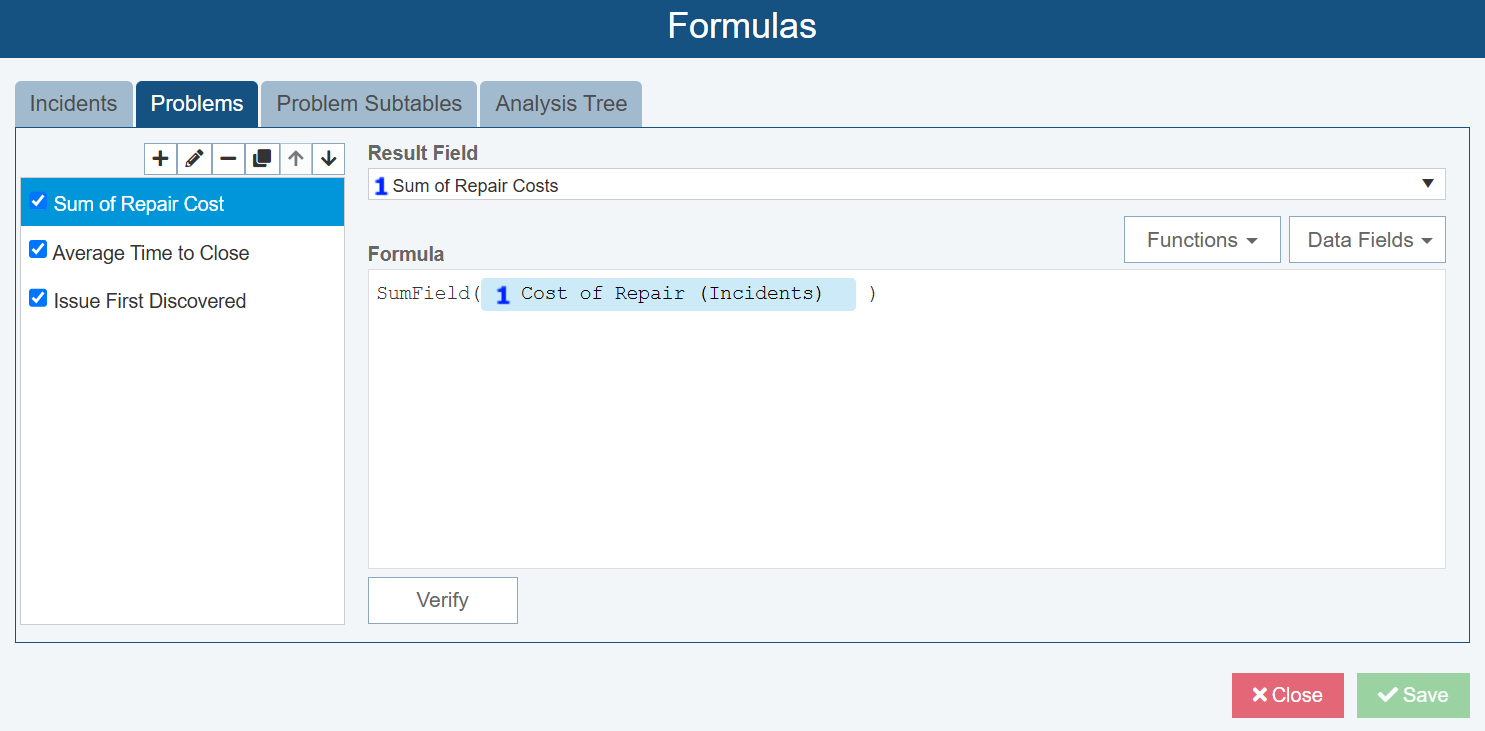
New Formulas capabilities allow you to set up custom calculations between Incidents and Problems – for example, summing the Cost of Repair for all Incidents associated with a Problem.
These are just a few of the many potential uses these new capabilities can offer. These enhancements offer even greater flexibility to Relyence FRACAS and can help ensure that issues are tracked through the appropriate processes efficiently and improving overall system reliability and product quality.
Warm Standby Redundancy Modeling in RBD Analysis
Relyence RBD combines advanced system modeling capabilities with a sophisticated calculation engine, enabling the computation of a wide range of time-based and steady-state reliability and availability metrics using both analytical methods and Monte Carlo simulations. With long-time full support for Series configurations, Parallel operating redundancy, as well as Hot and Cold standby redundancy, now with Relyence 2025 Release 1, Relyence RBD adds on the ability to compute Warm Standby redundant configurations.
Warm Standby redundant configurations incorporate backup components that are partially active and ready to take over in case the primary component fails. This can provide performance advantages compared to other redundancy types:
- Warm Standby failure rates are typically lower because they operate at a reduced state compared to Hot Standby configuration where backups operate at full capacity.
- Warm Standby backups have reduced component degradation due to operating at a reduced state.
- Backup components in a Warm Standby can offer quicker activation compared to a Cold Standby configuration because they are partially active at all times.
Overall, Warm Standby redundancies can provide balance between power usage and resource availability by keeping backups partially operational instead of fully active. This configuration is particularly beneficial in systems requiring high reliability and quick recovery, such as power systems, communication networks, and critical industrial processes.
Using Warm Standby in Relyence RBD
In RBD, modeling Warm Standby involves assigning appropriate failure rates to both the primary and standby components to accurately calculate system performance. Relyence RBD now supports Warm Standby calculations on both redundant blocks and branching configurations. To use Warm Standby, simply select Standby – Warm from the Redundancy Type selector then define the standby failure parameters for each block in the Warm Standby configuration by selecting the Set Standby Distribution checkbox.
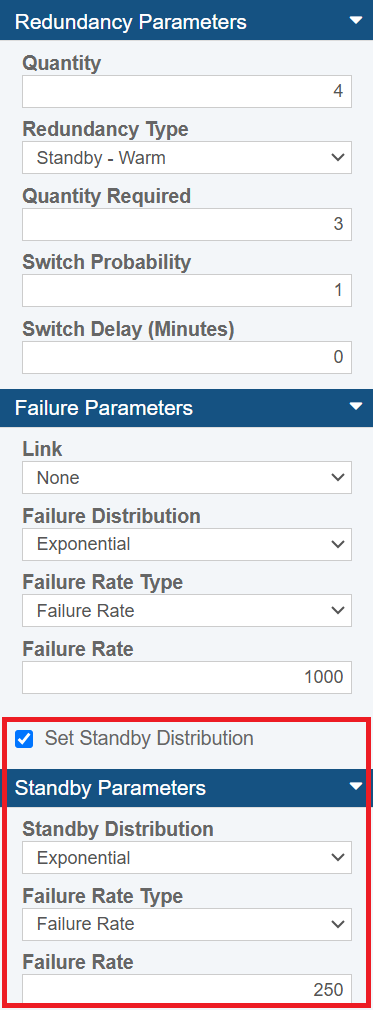
Relyence RBD now supports Warm Standby calculations on both redundant blocks and branching configurations.
And more!
Alongside the new features detailed above, Relyence 2025 Release 1 introduces several exciting enhancements to the Relyence Studio reliability and quality software suite, including:
- The ability to create and use multiple Libraries in Maintainability Prediction for Maintenance Tasks, FD&I Outputs, and Maintenance Groups
- Expanded filtering capabilities on FMEA Worksheets for Characteristics and Controls
- Ability to use hyperlinks on Announcements
- New option to sort Top Gates alphabetically in Fault Tree
Experience Relyence 2025 Release 1
With these exciting new features and enhancements, Relyence 2025 Release 1 is designed to meet the evolving needs of reliability and quality professionals. Whether you’re leveraging the power of Function and Failure Nets in DFMEA, optimizing your closed-loop corrective action process in FRACAS, computing your system’s failure rate in Reliability Prediction and RBD, or diving deeper into failure analysis with Weibull, this release provides a wealth of new capabilities for even more efficient reliability and quality analyses. For customers using the Relyence Cloud-Hosted solution, these exciting new features are available to you right now! If you’re using the Relyence On-Premise solution, you’ll gain access to these capabilities as soon as your installation is updated.
Whether you’re a current Relyence customer, a new customer, or considering becoming one, we’d love to hear from you! Your feedback is invaluable and plays a key role in helping us achieve our mission of delivering the best reliability software on the market.
We invite you to explore all that Relyence 2025 Release 1 has to offer with our completely free 14-day trial. Or to learn more details about these new enhancements, schedule a demo or contact our support team. We’d be happy to help show you why you can Rely on Relyence!