Failure Mode and Effects Analysis (FMEA) is a step-by-step approach used to identify potential failures in a design, product, service, or manufacturing process and analyze the causes and effects of those failures. The first well-known use of FMEA was by the U.S. military in the 1940s. A form of FMEA was used to minimize variation in the manufacturing process of munitions and was demonstrated to be an effective tool in reducing potential failures. Upon the proven success of FMEA, many industries, such as automotive and aerospace, began to adopt FMEAs to ensure the quality and reliability of their products. Today, FMEA is one of the most popular methodologies employed in reliability engineering.
Why Should You Use FMEA?
There are many benefits to using FMEA. In many industries, the reliability and quality of a product or process are of utmost importance. For example, in the healthcare or automotive industries, reliability is directly linked to safety, and a failure in a critical system can have severe consequences, such as accidents and injuries due to malfunction. Improved reliability and quality are the main reasons so many businesses turn to FMEA. Delivering reliable and high-quality products and processes directly impacts other important factors vital for business success, such as:
- Cost savings: Improving reliability and quality can lead to cost savings in the long run. High-quality products are less likely to fail, reducing the need for repairs or replacements. This, in turn, lowers overall maintenance and support costs.
- Operational efficiency: Reliable systems contribute to operational efficiency. Unplanned downtime due to system failures can disrupt operations, leading to lost productivity. Reliable products prevent potential failures and enhance overall system performance.
- Brand trust: Reliable and high-quality products or systems lead to increased customer trust. When customers can depend on a product to function as expected without frequent failures or defects, it enhances their approval and confidence in the brand.
FMEA is a highly effective, proven tool utilized in reliability engineering to systematically identify potential risks in a process or product. Rather than analyzing failures reactively when the options to manage the risks may be limited and repairs may be extensive, FMEAs offer a proactive approach to failure control. Engineers can create solutions to mitigate potential failure risks, ultimately leading to more reliable, safer, and more cost-effective products and processes.
What Are Some Key Elements of FMEA?
FMEA, as the name implies, is divided into two parts – analysis of (1) a system’s failure modes and (2) their effects. Additionally, key parts included in analysis are causes of the failure modes, risk assessment factors, risk levels, and recommended actions
Failure Modes, Causes, Effects
- Failure modes refer to the ways in which processes, products, or services could fail. Failures include aspects like defects and errors that affect customers.
- Causes identify the underlying reasons for the failure modes.
- Effects are the consequences of the failure modes on the process or system. Effects are the outcomes that result from a specific failure mode, such as waste or harmful outcomes for the customer.
Using a very simple example, a failure mode of a cellphone may be a damaged power connector. A cause could be the phone was dropped. One effect could be that the cellphone will not charge and be rendered unusable.
Risk Assessment Factors
Once the causes and effects are recorded, engineers can determine the risk associated with each item. Failures are assessed based on several factors so that those of utmost concern are prioritized and eliminated.
The following factors are often used to assess risk and are commonly described by a numerical value. The numerical rating systems may be 1-10, a probability value, or even a custom rating system. Note that numerical rating systems are not required, sometimes simple High/Medium/Low designations are used.
- Severity: Severity indicates the seriousness of a failure with a focus on the consequences. The higher the number, the greater the severity.
- Occurrence: Occurrence indicates how frequently a failure is likely to occur. The higher the number, the greater the probability of occurrence.
- Detection: Detection indicates how easy or difficult it is to identify a failure. The higher the number, the less likely the failure is to be detected.
Risk Level
These factors are then used to determine the risk level. Risk levels are used to prioritize the failure modes for elimination or mitigation efforts. Risk can be assessed in more than one way. Two of the most common approaches for risk assessment are:
- Risk Priority Number (RPN), most commonly a numerical value between 1 and 1000, is calculated by multiplying severity, occurrence, and detection scores. RPN is a widely adopted method for risk assessment.
- Action Priority (AP), was introduced in the AIAG & VDA FMEA Handbook and is a value that considers severity, occurrence, and detection scores with varying emphasis to determine a rank for each failure mode (High, Medium, and Low).
Our informative white paper provides details the best strategies for risk assessment with FMEAs.
Recommended Actions
After ranking the potential problems, engineers can determine which items to focus on and come up with an action plan.
- Recommended actions are specific measures proposed to address the identified risks associated with potential failures. These actions are developed to reduce the risk assessment factors of the failure modes and improve the overall reliability and performance of a process or system.
When Is FMEA Used?
One benefit of FMEA is that it can be accomplished as often as needed at various stages in the product or process lifecycle.
- Designing and developing a new product or process: FMEA is commonly used during the design and development phase of a product or system. This helps to identify potential failure modes early in the design process, allowing engineers to make informed decisions to improve reliability and performance before a solution is released. If a failure is uncovered after a process is in place or a product is in the customer’s hands, the costs to fix the issue are much higher. When a high-risk potential failure is identified early on, mitigation can be done prior to manufacture or assembly.
- Introducing new variants or applications: When new elements are put in place or a product or process is applied in a new way, new risks are often introduced. FMEA is valuable for evaluating potential risks associated with the changes and the impact of these changes on existing processes or systems.
- Analyzing failures of an existing process or product: When there are quality issues, incidents, or failures, organizations may perform FMEA to investigate the root causes, identify new failure modes, and implement corrective actions to prevent similar issues in the future, which all strengthen the overall quality of the system.
- Performing continuous improvement initiatives: FMEA can be performed periodically throughout the life of the process or product. Regular reviews and updates to FMEAs ensure that risk assessments remain relevant and effective, and organizations stay proactive in addressing emerging issues. This is crucial in industries where consistency, reliability, and quality are of utmost importance.
While FMEA is often performed at earlier stages of product or process design, it is recommended to perform FMEA regularly during the lifetime of a product or process to maintain reliability and quality objectives.
What Are Different Types of FMEA?
There are multiple types of FMEAs, all of which share the same goal of detecting, mitigating, and/or eliminating critical risk events. However, the two most commonly used are Design FMEA and Process FMEA. Both seek to identify failures and minimize their chance of occurrence, but they are used in different situations.
Design FMEA
Design FMEA (DFMEA) is an organized approach that aims to identify and mitigate potential failure modes that may arise from a product design. DFMEA is used to evaluate product malfunctions due to factors like material properties or interfaces with other components and systems. It is typically performed during the product design and development phase so that failure modes can be detected and mitigated before the product is manufactured. DFMEA is primarily concerned with meeting functional and performance requirements.
For example, a potential failure mode discovered during the design phase of an automotive transmission system might be material fatigue in the gear shaft. To perform a DFMEA, engineers would assess the cause (e.g., inadequate material strength), and the potential effects this failure can have on the overall system (e.g., transmission). They would then assign a risk rating and determine an action plan to mitigate the material fatigue in the gear shaft, such as conducting material testing.
Process FMEA
Process FMEA (PFMEA) is like DFMEA in purpose, but it is performed on a process as opposed to a product. PFMEA identifies and evaluates the potential failures in the operational processes involved in producing a product, such as human factors, environmental factors, and the materials used. It finds problems in a process that impact quality and ensures processes are well-controlled. It is typically conducted during the manufacturing or implementation phase.
An example of a process for an automotive part may be grinding a surface to prepare for painting. A potential failure mode may include uneven surface finish. While the design is safe, the uneven surface causes cracks in the paint. Like DFMEA, to perform PFMEA, engineers assess the potential causes and effects of the failure mode, classify the risk level, and come up with an action plan to mitigate that risk.
Organizations can use both types of FMEA to comprehensively manage risks throughout the entire product development and production process.
What Does the FMEA Process Look Like?
Each company has its own process for conducting an FMEA based on their specific needs, but the general steps of the process are consistent.
Step 1: Define the Functions or Process Steps
You may choose to analyze all functions or process steps or decide to evaluate specific elements you feel are problematic, more complex, or pose more potential risk. DFMEA begins by breaking down of all the individual components of a product, such as the hardware components that comprise a system. The breakdown can be as detailed as needed. For a product, DFMEA may begin early in the design phase when only a high-level breakdown is available, then as the design matures, the components may be broken down into lower-level elements. For PFMEA, rather than breaking down the product into components, processes will be broken down into individual steps.
Step 2: Determine the Failure Modes
Systematically go through the elements and identify all the ways in which failures could happen for the function or step. For example, if the function is deceleration, a failure mode could be brake pad wear.
Step 3: Analyze the Causes and Effects
Identify the potential causes of each failure mode (e.g., normal wear and tear). This helps in understanding the root causes of potential problems, which is essential for developing corrective and preventative action plans. Also, identify the effects or consequences of each failure mode on the overall system (e.g., reduced braking efficiency). There may be more than one cause and more than one effect for each failure mode.
Step 4: Rank the Risk Level
Determine the risk level associated with each item. This will help prioritize the list of failures and the necessary changes to the product or process to lower the risk. Evaluate and assign a severity rating for each failure mode based on the impact of the failure on the overall system. For example, if using RPN, assign ratings for severity, occurrence, and detection and then calculate the RPN for each failure mode by multiplying the severity, occurrence, and detection ratings.
Step 5: Establish the Recommended Actions
Based on the established risk assessment criteria, determine which items to focus on for improvement. Define the corrective actions needed to lower the risk associated with failures. This could involve updating design specifications, modifying processes, or enhancing quality control measures. In some cases, you may determine you can eliminate the risk, while in other cases, you may only be able to mitigate the level of risk.
Step 6: Implement the Recommended Actions
Recommended actions are added to the FMEA and assigned to team members to complete. Implement the recommended changes to address the identified issues and update the FMEA to describe the work done and when it was completed. Then, reassess the items based on the process or design change.
Monitor for Continual Improvement
An important aspect of FMEA is that they are considered living analyses. In some cases, FMEAs may be archived if a product is retired, or a process is no longer in use. However, for products and processes still in use, it is beneficial to periodically reassess the FMEA to ensure that the implemented corrective actions are effective and make any updates as new information is incorporated.
For a real-world example of the FMEA process, you can read our six-step blog post or view the six-step video overview.
What Are Some Tips for Conducting FMEA?
As you perform FMEA, there are a number of considerations to keep in mind that will help you get the most from your analysis.
Tip 1: Clearly Define the Scope of Your Analysis
Set the scope of your FMEA to avoid unnecessary complexity by identifying and focusing on specific functions or processes that are critical to the quality of your product or process. Without a clear scope, the team may be overwhelmed by the volume of potential failure modes to consider. Furthermore, by having a well-defined scope, resources such as time, personnel, and data can be optimized. Unnecessary analysis of non-critical elements can be avoided, allowing the team to allocate resources more efficiently.
Tip 2: Employ Visual Tools
Visual tools can be very effective for FMEA team members. They can provide an overview of the system being evaluated in a concise and easily understandable way.
For DFMEA, boundary diagrams illustrate the boundaries of the system being studied and provide a clear overview of its interactions with external elements. A boundary diagram is helpful to get the team on the same page and communicating effectively throughout the FMEA process. Creating a visual representation of a system helps define the scope by showing the major components involved and the interactions between components and external factors, such as environmental factors, which can aid in identifying potential failure points.
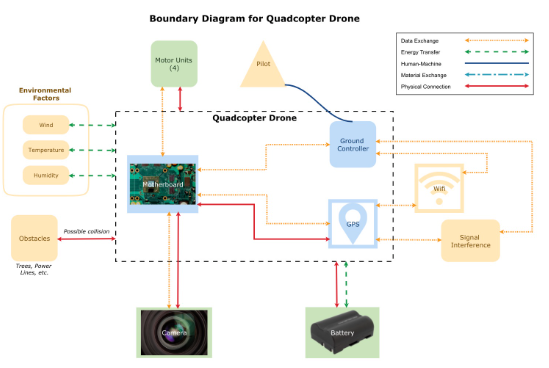
Example Boundary Diagram
For PFMEAs, P-Diagrams and Process Flow Diagrams are helpful tools. P-Diagrams are used to conduct an upfront assessment that your required outputs are met considering all inputs. Process Flow Diagrams, or PFDs, are a visual representation of a process including all the steps and their sequence. PFDs can help in early analysis stages to efficiently communicate the entire process flow.
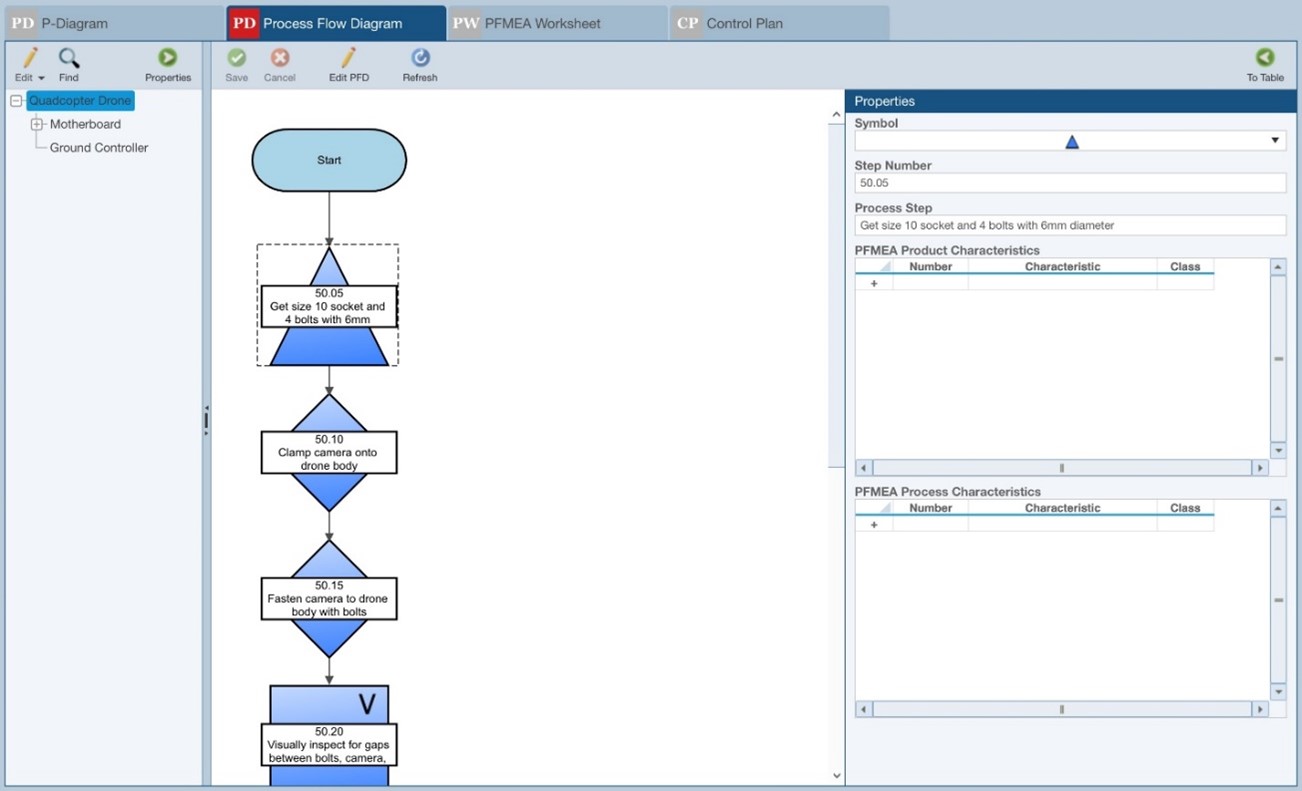
Example Process Flow Diagram (PFD)
Tip 3: Consider Using a Standardized FMEA Method
The flexibility inherent in Failure Mode and Effects Analysis enables organizations to develop a customized process to meet their specific goals and objectives. However, many analysts choose to use an established FMEA methodology, such SAE J1739, ARP5580, or MIL-STD-1629A, as a basis for their analyses. In some cases, using a standard FMEA process may be required for regulatory compliance. In either situation, choosing a standard FMEA methodology ensures that the terminology and criteria used are consistent. This consistency promotes a common understanding of the analysis and its results. Importantly, standards allow for flexibility in implementation which enable analysts to adapt the process to fit their requirements. For this reason, FMEA standards are oftentimes used as a starting point and then modified to meet an organization’s specific needs.
Tip 4: Prioritize and Focus on High-Risk Items
Resources, such as time, manpower, and budget, are finite. Focusing on addressing high-risk items allows resources to be allocated to areas where they can have the most significant impact, leading to a more effective risk management process. This involves prioritizing failure modes with the highest risk metrics that have been determined by the organization.
Tip 5: Utilize a Team-Based Approach
The most effective analyses are those that are conducted using a team-based approach. It is important to involve team members from across your organization in identifying the failure modes of the product or process. Having multiple set of eyes can uncover hidden risks and improve the overall quality of the analysis. This is especially true if the team consists of members from different parts of the product or process lifecycle, who can bring a diverse set of expertise. In addition, tasks can be distributed among team members based on their expertise and availability, accelerating the overall analysis process. You may utilize a trackable, approval-based control of your FMEA process that defines a workflow that matches your internal process, notifies team members to inform them of events that occurred, and requires approval from team leaders as needed.
Tip 6: Review and Update Your FMEA Regularly
FMEA is a part of a continuous improvement process. Any changes to the design or process may introduce new failure modes and impact the system. Regular updates to the FMEA ensure that the current state of the system is reflected. Regulatory requirements and industry standards may change over time as well, requiring FMEA to be updated to ensure compliance with the latest standards. In addition, teams may gain feedback from incidents that occur during the operation. It is important to build on knowledge based on past experiences or near-misses that can identify new failure modes and risk factors in order to prevent the recurrence of similar issues in the future.
By implementing these tips, organizations can ensure that their FMEA process is effective in not only identifying and mitigating the risks but also adaptable to the evolving dynamics of their systems and environments.
What Features Should You Look for in FMEA Software?
While it is possible to use traditional tools like Excel for FMEA, there are many limitations to its capability. For example, using Excel can be a time-consuming and complicated experience with manual entry and copy/pasting. There are many benefits to using a software tool that is designed for FMEA, as it provides a comprehensive and efficient tool for effective risk management. In addition to some key features noted below, read our detailed blog post on how to select the right tool for your Failure Mode and Effects Analyses.
Scalability
Your FMEA software tool should be designed to accommodate the evolving needs of the organization. As an organization grows, the complexity of its processes, products, or systems also increases. Scalability is crucial when organizations conduct multiple FMEAs concurrently. Your software tool should support the management of multiple analyses across different projects without compromising the efficiency and speed of the process. In addition, it should be able to manage a growing user base and handle an increasingly larger volume of data over time. This ensures that the software remains efficient even as the complexity and scope of analyses increase.
Efficient Data Handling
Look for FMEA software that automates certain processes, such as data entry, calculations, and other repetitive tasks, which enhances efficiency. For example, for data that is often used across analyses, manually entering the same set of data can take up unnecessary time and resources. Features such as auto-complete, automated data handling, coverage verification, and reusability can not only prevent repetitive work but also ensure consistency in your data and reduce the likelihood of omissions and errors.
Seamless Collaboration
Collaboration features within the FMEA software streamline communication among team members. For example, feedback mechanisms that allow users the ability to comment and share information contribute to better communication and decision-making. Other features, such as a built-in workflow and approval process, can keep team members on task and informed. A benefit of a cloud-based solution is that it enables easy access to FMEA data from different locations and devices, fostering collaboration among distributed teams.
Customization Capabilities
Organizations often have unique processes, workflows, and methodologies. Further, different industries have specific standards and regulations governing risk management. Customization enables the adaptation of the FMEA software to match the specific processes and workflows followed by the organization. This includes the ability to customize fields, risk criteria, and reporting formats. Organizations may need customization abilities even within their own group. For instance, they may use a variety of processes for different aspects of their operations, and the software should be sufficiently flexible to be tailored to the groups’ needs.
Performing an FMEA can involve keeping track of large amounts of data and processes, and a good software tool should effectively support the potential complexities of FMEA.
Contact Us
Relyence FMEA is the most complete and powerful software package available for FMEA. Various features available in Relyence accelerate and support FMEA analysis, enabling organizations to efficiently identify potential failure modes and enhance the overall quality and reliability of products or processes.
To learn more about our FMEA software and how it can work to support FMEA in your organization, contact us, schedule a free personalized virtual demo, or register for a free trial to see Relyence FMEA in action.